It is an Italian symbol, currently also sustainable and 100% electric. For the second consecutive year, in fact, Nuova 500 by Fiat has conquered the title of “best small electric car” at “What Car? Electric Car Awards 2022”, due to its performances, the interesting price and the iconic design.
At present the Nuova 500’s list of trophies counts 33 international prizes awarded by the public and by sector experts in nine Countries. A success confirmed by sale outcomes: in just two years, it has been chosen by over 100,000 customers worldwide; it is the best-selling electric vehicle in Italy and in Germany and ranks on the podium in France and in Europe. «Diamond tip of our electrification strategy, then, the new Nuova 500 will soon land in the United States, prosecuting its global course outside Europe, after crossing Middle East, Brazil and Japan», stated Oliver Francois, FIAT CEO and Stellantis Global CMO.
Electrification strategy. Do you know the best small electric car?
The production of BMW i7 is starting
The production of the new Series 7 BMW and of i7 inside Dingolfing factory has started. The investment to adapt the plant to the production of the new sedan, offered also with Plug-in and 100% electric powertrains, the company has invested 300 million Euros.
The transformation towards a “BMW iFACTORY” is in progress, with much automation and optimization of processes, and to have more flexibility the new Series 7 is assembled on the same line of BMW Series 5, of Series 8 and of the fully electric BMW iX.
The direction is traced: by the end of 2022, one BMW out of the four leaving Dingolfing is expected to be equipped with an electric motor.
The electric BMW i7 sedan will be proposed in the xDrive60 variant with double electric motor able to deliver on the whole 400 kW (544 HP) with 745 Nm of torque. Due to the 101.7 kWh battery, the autonomy according to the WLTP cycle reaches 625 km.
Electric motors and cybersecurity
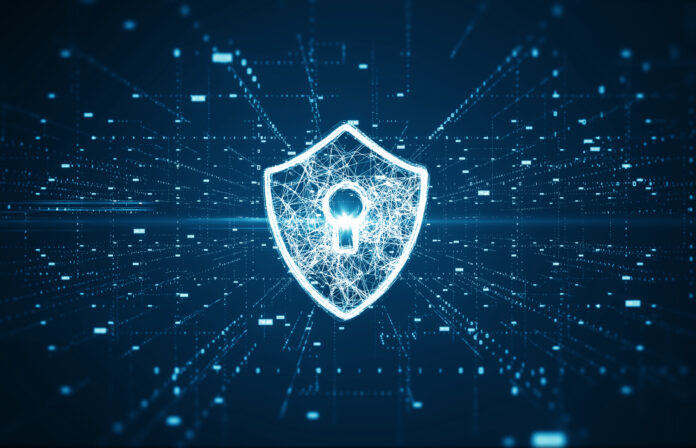
The rise of electronic components in cars subjects them to a higher hacker attack risk. Currently, the onboard electronics constitutes 35% of the car value, with the prospect of reaching 50% within next ten years. Consequently, digital attacks will be favoured by an ever-rising IT complexity, but with a lower risk perception. As a matter of fact, already today acts of IT piracy in the automotive field are neatly rising, but underestimated.
For this reason, HSB Munich Re has recently carried out an investigation that has surveyed that 37% of the American owners of an electric car are very worried about their cars’ net safety.
Given the acceleration to the shift to electric cars, protecting these vehicles’ IT safety is certainly fundamental. For this reason, the University of Georgia has published a guide concerning electric cars’ information safety.
While previously risks were connected with warranty frauds or mileage alteration, in recent years privacy damages have emerged, cyber blackmails and warfare.
If a hacker attack against one’s own vehicle takes place, some other problems will occur, such as speed and acceleration damaged, decrease of the vehicle’s efficiency, batteries fully discharged and data unreadability on the display.
All signals exerting a negative impact on the vehicle’s safety. A list of suggestions to limit car hacking risks? Monitoring the onboard diagnostics, installing only reliable hardware, performing code reviews, updating software safely and installing a monitoring system of the cyber security.
France, Stellantis carries on the electric transformation
Whatever action by Stellantis has an unbelievable mediatic effect and can determine real changes of paradigm. Well, during one of his recent visits to manufacturing plants at Trémery-Metz in France, the CEO Carlos Tavares highlighted how the transformations of plants demonstrate the progresses made by the company towards the achievement of electrification targets expressed in the Dare Forward 2030 plan.
Let us remind them: the 100% coverage of sale mix with battery electric vehicles for cars (BEV) in Europe and by 50% of the sale mix of BEV with cars and light commercial vehicles in the United States within 2030.
Since 2018, the company has invested 2 billion Euros in French manufacturing sites. Well, through the investments in two key joint ventures at Trémery-Metz, Stellantis has deployed a vertical integration strategy aimed at increasing the control of the global electrification value chain. It is Emotors, a 50% joint venture with Nidec Leroy-Somer Holding, which in the current year will start the production of a range of forefront electric motors at Trémery factory, in the past the biggest manufacturing plant of diesel engines in the world and now the first Stellantis structure that produces electric motors.
The other is e-Transmissions, a 50% joint venture with Punch Powertrain, funded with an investment worth 57 million Euros, until now it is focused on the production of the next generation of electrified dual clutch transmissions (eDCT) at Stellantis factory in Metz.
The plant, renowned for its competences in the production of transmissions, is expected to increase its yearly production up to reaching about 600,000 eDCT within 2024 for the hybrid portfolio of Stellantis.
The Emotors M3 will be the first electric motors in the range.M3 will supply an efficient and economically competitive electric traction system, designed to operate with 400 V voltage and supply a power of 115 kW, which will make its debut on a Stellantis BEV by the end of 2022.
The eDCT transmission is available with two electrification levels, 48 V and 320 V, and it can be used for hybrid and PHEV applications.
Electric motors and digitalisation: quo vadis?
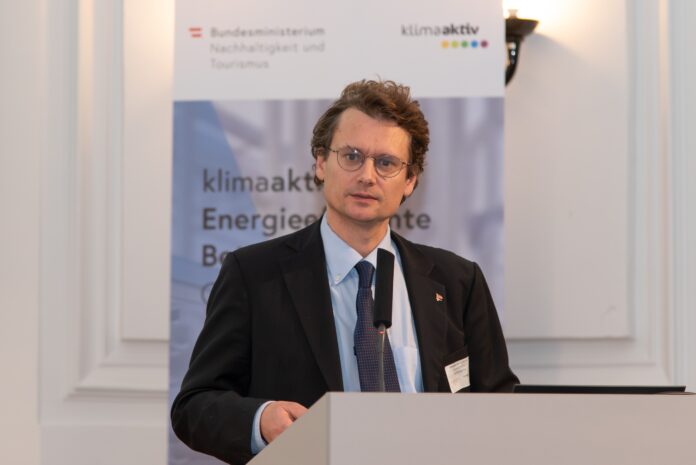
Electric motors and motor-driven systems in industrial and infrastructure applications are responsible for 53% of the world’s total electricity consumption and about 70% of industrial electricity consumption.
New technologies offer the potential to reduce the energy demand of motorised systems across the global economy by 20-30%, with short payback periods. Reducing energy consumption means at the same time reducing emissions related to energy production. As sustainability is now the main driver of innovation and European legislation, employing technologies that allow an increase in efficiency means not only direct savings for the system owner, but also bringing the system in line with legislation and therefore safe for the future. Ultimately, it means building systems that are ‘future proofed’. Today, the digitisation of components, machines and systems is undoubtedly one of the faces of innovation in industry. On-board sensor technology, the cloud, and the use of advanced data analysis tools enable optimised operation of components, and thus also of motors, and improved performance.
Digital Production Technologies in Electric Motor Driven Systems: a project
The potential for energy efficiency and thus savings that could result from the digitisation of electric motors is therefore high. Within the IEA – International Energy Agency – there is a technology collaboration programme called 4E EMSA (Electric Motor Systems Annex) that works on the evaluation of specific developments in the field of industrial digitisation of electric motors.
This programme aims to increase worldwide awareness of the efficiency potential of motor systems and provides guidance and tools for harnessing the energy performance of new and existing motor systems worldwide.
As part of its work on the use of digital technologies for electric motor systems, it recently conducted a survey to understand the level of deployment of digital technologies on motors in Technologies in Electric Motor Driven Systems.

In dialogue with Konstantin Kulterer, Senior Expert in Commerce and Industry at the Austrian Energy Agency, the agency leading the project.
Why a survey on digitalization of electric motors? What was the main goal of the survey?
This survey is part of a study into the potential impact of digital technologies on the electricity consumption of electric motor systems in industrial companies. The research seeks to provide further insights to decision makers in industry and governments on what digitalisation can mean in energy efficiency of motor systems and energy transition in broader perspective.
We wanted to know which digital technologies are already used in connection with electric motor driven system and how high the expected savings from using these tools are expected to be.
Furthermore, we asked for the main advantages and disadvantages when using these technologies but also for barriers and enablers for these technologies. Furthermore, we asked which could be the main instruments to overcome these barriers.
The respondents are electric motors system user or producers of electric motors?
Both. The survey was mainly answered by companies from the manufacturing sector (27%) and professional, scientific and technical activities (27%). Roughly half of the companies were small companies; one third of the companies were large organisations. But we do not have an evaluation how many motor producers answered the questionnaire.
Some of the company interviewed already use digitalization, some others plan to do it in the future. Where will they use more digitalization? In their production process or in their products?
In principle, digitalisation technologies will be mainly used for superior production efficiency, more flexible systems and better control, as well as higher system availability through predictive maintenance. This means that industrial end users will use digital technologies to improve their production processes by increasing transparency. For that they also will use the features of the products (e.g. pre-installed sensors or information from the variable speed drive), when manufacturers of motors and drives provide these features.
In your opinion which general statement can be made on digitalization of electric motors today?
There is a clear awareness of advantages in digitalisation of electric motors today in the motors expert field. Especially condition monitoring for detecting faults before they happen and avoid production stoppages and/or avoid expensive repair procedures. Industrial end users are also becoming more aware of this feature. For use of digital technologies for energy saving we are in the status that monitoring of energy consumption of these systems is connected to the general energy data management system of companies. But I think the use of this application should and can be improved, e.g. with calculation and evaluation of benchmarks to monitor the efficiency and with introduction of target levels for the efficiency.
Concerning knowledge of technologies, I think that in smaller companies knowledge about digital technologies in general seems to be lower, whereas in bigger companies special teams can deal with that issue. In general, there are a lot of different providers out there, that can help but currently each company has to find its specific solution which partly has to be developed for them during project implementation.
What is the main result of your survey? And of the ongoing project until now?
Around half of respondents of the EMSA survey consider the saving potential to be between 6 and 20% through the use of digital technologies (Stand: end of 2020). Among others, the lack of qualified staff is perceived as the main barrier to a greater uptake of digital technologies. Therefore, the development of training programmes is important, and guidance for SMEs on how digital projects can be implemented in this area and what benefits can be gained from them. The standardisation of protocols and data access as well as the clarification of data ownership are seen as important tasks of policy and standardisation work. Nonetheless, to solve the problem of security or confidentiality of data in cloud applications, good technical solutions for cybersecurity are also critical.
Which digitalization technologies are currently mostly used?
Industrial users are currently especially using smart sensors, smart control, and continuous monitoring as digital technologies, in conjunction with motor driven systems.
What is the status of digitalization of electric motors?
Especially, in compressed air systems, meaning bigger stations with new equipment, the digital technologies are already quite advanced. For fan and pumping systems though technologies are available the possibilities are not really used and in a lot of cases not implemented. E.g., in a Swedish survey in connection with our project one third of the companies said that they do not gather any data for fan systems.
What are the main opportunities of digitalization of electric motors, in your opinion?
Information and communication technology should be used firstly as the enabling technology to obtain basic data on performance, operating time and energy which is not available in a lot of companies. Yet, while digital technologies can help identify opportunities, energy savings will only be realised by acting on that information. In the future I think digital technologies will be able to detect inefficiencies in motor systems and react accordingly, automatically.
The asphalt that electric cars like
This is a piece of news that can inspire electric market players for the potential synergy with the induction recharge technology for electric cars Dynamic Wireless Power Transfer (Dwpt). It is a new recharge frontier currently implemented in the experimental circuit “Arena del Futuro” of about 1 km, along A35 Brebemi motorway.
This technology allows the recharge of electric vehicles while travelling on dedicated lanes, thanks to an innovative system of coils positioned under the asphalt that directly transfer the necessary energy to the vehicles in transit.
The installed Dwpt technology is powered by a megawatt of energy and relies on 5G network for vehicles’ communication with infrastructures. The energy is provided by direct current net and photovoltaic plants, it is transformed into alternate with a suitable frequency for the wireless and then transferred to “coils” positioned under the asphalt. The technology can be adapted to all vehicles equipped with a special “receiver” able to transfer the energy coming from the road infrastructure directly to the electric motor, extending the autonomy and protecting the vehicle battery’s charge.
The stop to thermal motors is postponed
The market of electric motors and related components is looking with extreme attention at the official decisions concerning the stop to thermal cars, sanctioned by EU for 2035. The latest news about that reports an Italian Government that is going to propose the postponement for the complete stop to thermal cars by 2040, decreasing carbon dioxide emissions by 90 % within 2035. It is a political decision taken in common agreement with the national companies in the supply chain, choice shared also by other States belonging to the European Union, such as Bulgaria, Portugal, Romania and the Czech Republic.
It is certain that this acceleration to a final date is causing a lot of turmoil in the specific market and in all induced activities, final consumers included.
Innovation in the recycle of electric motors
In an industry that is expected to be increasingly green, recycling is a crucial theme, also and especially for electric motors. And there are no doubts about possibility of processing electric motors since up to 98% of its overall weight can be recovered, transforming it into secondary raw material. Concerning this, among the outstanding companies ranks the Italian Panizzolo, in Padua province, which ensures high-performance and wear-resistant system. The Italian player in the recycling system has recently communicated to the market to know only too well the issues related to wear and strong stress that the components, welds and steelwork are subject to. This is why the hammers and armours of Panizzolo are made in special anti-wear castings specifically designed jointly with the University of Padua – for the processing of bulky waste. The sorting of the outfeed granule is just as important.
The company invites to discover the mega 1100 hammer mill with electric power of 355 kW and a production up to 22 tons/h.
A new type of electric magnet-free motor?
The German manufacturer MAHLE, with headquarters in Stuttgart, is currently developing a new type of electric magnet-free motor. Its central feature is the inductive, and then contactless, power transmission, which allows the motor to operate wear-free and to be particularly efficient at high speeds.
Concerning this, the efficiency exceeds 95% in almost all operational points, a level that previously was reached by Formula E race cars only. In this way, MAHLE has succeeded in matching the highlights of electric motors’ various concepts in a single product.
It is an easily scalable development, which can be used by small cars as well as by commercial vehicles.
Moreover, the new electric motor is characterized by a long service life in time, because the necessary transmission of electric currents between rotary and stationary parts inside the motor is contactless and then wear-free. This makes the motor maintenance-free and suitable for a broad range of applications.
Michael Frick, Chairman of the MAHLE Management Board (ad interim) and CFO said: «With our new electric motor, we’re living up to our responsibility as a sustainably operating company. Dispensing with magnets and therefore the use of rare earth elements offers great potential not only from a geopolitical perspective but also with regard to the responsible use of nature and resources».
Dr. Martin Berger, Vice President Corporate Research and Advanced Engineering at MAHLE added: «Our magnet-free motor can certainly be described as a breakthrough, because it provides several advantages that have not yet been combined in a product of this type,” says “As a result, we can offer our customers a product with outstanding efficiency at a comparatively low cost».
Bentley is recruiting 100 engineers for its electric race
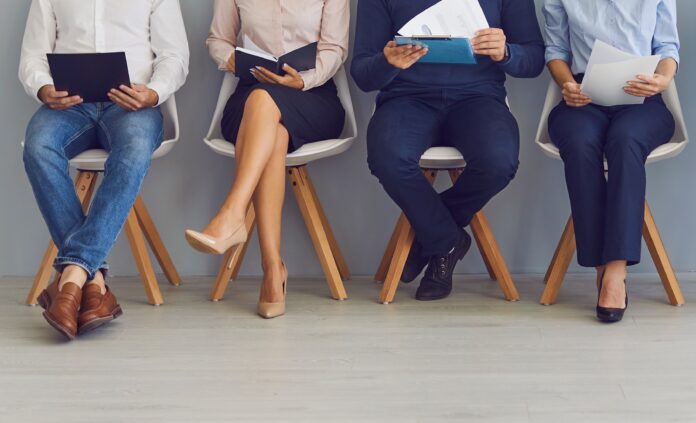
Bentley Motors’ recruiting campaign is underway for 100 talented engineers in the ambit of its Beyond100 strategy: the brand will release a new electric model every year starting from 2025.
The new engineers will support the implementation of the ambitious Five-in-Five plan, redefining Bentley’s credentials as reference manufacturer in the sustainable luxury mobility.
Therefore, they are searching for engineering professionals trained in the electric ambit because Bentley aims at the complete electrification of its product range within eight years.
Besides the need of electric engineers, next offers will concern the research and development ambit, from UX/UI engineers inside concepts and design, to Design Managers in the development and validation of parts and entire vehicles, to framework engineers who work at the prompt vehicle production.
«Bentley is in the middle of the most significant transformation phase in the company’s long illustrious history. We are searching for real innovators, who can create the new future of automotive, support our product ambitions and shape our Beyond100 vision while we are focusing on the leadership inside the luxury sustainable mobility», stated Matthias Rabe, member of Bentley’s research and development board.
Although roles are located at Bentley’s Crewe headquarters, the company has introduced the hybrid work, a combination of activity inside brand-new forefront engineering offices and smart working.
It is not fortuitous that at the beginning of the current year Top Employers Institute has appointed Bentley as “Top Employer“, only automotive manufacturer headquartered in the United Kingdom for the eleventh consecutive year, underlining Bentley’s approach to wellbeing, to values, to ethics and to employees’ integrity, in addition to Bentley’s attention to sustainability, digitalization and diversity and inclusion.