50 years of experience have led the Vignati Group to develop strict processing methods with quality meeting the highest standards, with technical skills enabling it to assist customers even in conceiving and creating complex subassemblies. The Vignati Group is specialized in the production of complex technical components, including the production of moulds and dies. Its main areas of business are: appliances, automotive, electronics and electromechanics; medical; telecommunications.
The Vignati Group provides prototyping services through its prototype manager: analysis of details prior to industrial launch; launch of mould and die design; validation of designs; production of moulds and dies; testing and compilation of specific technical dossier; product qualification; assembly as customer requirements; correct management of the industrial engineering process is the key to reducing technical risk, thus reducing costs and meeting programming deadlines and quality standards; partnership with high-level laboratories to offer services marked by active participation in the development of the component and its function right through to the creation of the subassembly, featuring quality and performance without the high costs.
Vignati Group, complex technical components
Solutions for the emerging trend towards e-drive modules
Next to liquid sealants, thermal interface materials, adhesives and impregnation resins for new-generation battery packs, Henkel is leveraging existing and new products and technologies for the emerging trend towards e-drive modules combining electric motor, power electronics and gearbox in one integrated e-axle unit. In addition, customers are also supported with appropriate design guidelines and recommendations for process requirements including equipment enabling automated high-volume production. Henkel’s portfolio for the entire value chain of e-drives manufacturing is focused on six key application areas: liquid gasketing, potting, pcb technologies, magnet bonding, impregnation service and parts cleaners and lubricants.
A polyacrylate technology – Loctite AA 5831 – is used for protection and fixation of parts in the e-motor or in the conversion electronic control unit. The compound has an ideal fit in large-series potting operations and cures within seconds under UV light and moisture. For e-drive stator coil potting applications, Henkel offers the two-component epoxy technology of Loctite PE 8082 which has a thermal conductivity of 1 W/mK, resulting in a significantly reduced working temperature. In addition, it shows outstanding oil resistance. Loctite EA 9497 is used for the bonding of magnets inside the e-motor. The two-component epoxy adhesive has proven its long-term reliability in this application segment, combining a wide operating temperature range of -55°C to +200°C with high mechanical strength as well as good chemical and oil resistance. With its added thermal conductivity, it also supports a more efficient thermal management. Parts cleaners and lubricants: Henkel’s range of machining products along with parts cleaners help to maintain a cleaner part through the entire process to ensure tight tolerances and reduce residues on parts, especially when used on sensitive e-drive modules.
Hypercar: an electric luxury
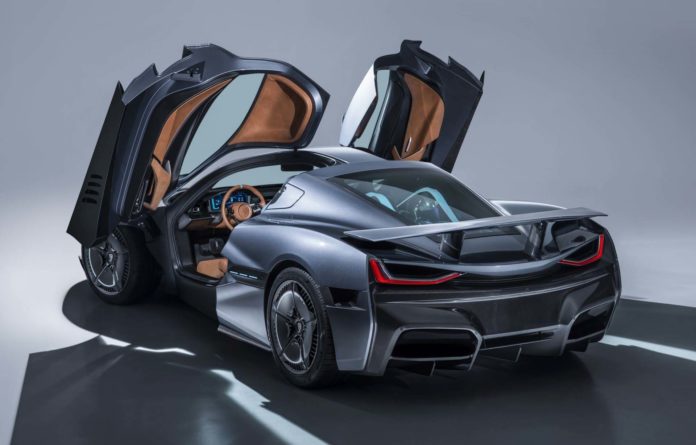
Hypercars push the exclusivity concept to extremes: they are vehicles that are part of very limited series, with sports aesthetics and exasperate performances, by far exceeding conventional sports cars. Often, hypercars propose innovations in advance compared to the other cars and they are used as test bench to diffuse determinate technologies on more “reachable” vehicles.
We are speaking of a parallel world, of an extra-luxury market that exists thanks to an elitist niche of people looking for adrenaline, fond of motors and performances, willing to pay very high amounts to own and to drive vehicles that represent the utmost expression of the automotive technology. Hypercars satisfy on four wheels man’s natural bent for overcoming limits and it is unavoidable that such extreme cars make us dream, engaging in the design smart minds of skilful and enthusiastic engineers like Francesco Mastrandrea from AVL, the interviewee of these pages.

What a hypercar is
The engineer Francesco Mastrandrea has helped us to define “hypercars”: vehicles that belong to very limited series, with sports aesthetics and exasperate performances, by far exceeding the traditional sports cars. «These cars – the engineer Mastrandrea explains us – must be framed in the context of their historical period and borders are anyway undefined. A car considered hypercar in the Eighties, like for instance the F40, today would be deemed “just” a sports car, neither with particular qualities; let us think that a current Alfa Romeo Giulia Quadrifoglio Verde, apparently a common sedan, has 510 horsepower and overall performances that exceed a hypercar dating back to 25 years ago».


How were they born and what is their origin? The motivation should be sought in the precise essence of man and his will of overcoming the imposed limits. There have always been people who are not satisfied with standard vehicles and the hypercar concept was devised precisely with the advent of cars; we remember that in the Sixties there were already several brands that modified “standard” cars to create unique models intended for exclusive users. «Often, hypercars propose innovations in advance compared to the other cars and they are often used as test bench to diffuse determinate technologies on more “reachable” vehicles. “LaFerrari”, for instance, with its hybrid powertrain has anticipated some years earlier the use of this technology on the rest of Ferrari range».


for each wheel.
Hypercar VS Supercar
If performances, very high cost and sports aesthetics might almost be shared by hypercar and supercar, there is a neatly different factor: the production modality.

«I had the lucky opportunity – told us the engineer of AVL – of living some phases of the creation of these vehicles. Hypercars further heightens the exclusivity concept: very few are produced upon customers’ specific demands and a direct relationship between buyer and manufacturer often emerges, with production logics that are more similar to the ones of an expert artisan.
Another differentiating factor concerns the availability on the market. Sport cars, even if with long wait times and for few people, are accessible because they are anyway catalogue cars. The price as well shares in creating a gap between the supercar and the hypercar: if the cost of a sports car range from 300 to 500,000 euros, a hypercar generally starts from one million of Euro, with some small exceptions. «Not many people in the world can afford it but more than we can imagine. They have manufactured 500 Ferrari hypercars whose cost is 1.7 million Euros and they were fully booked before the production started. In this market slice everything is relative: if you have already a yacht moored at the port and other three Ferrari in the garage, spending almost 2 million Euros for a car is quite coherent, obviously in that context».
Another aspect that characterizes this segment is the second-hand market that has opposite logics to the “traditional” one”. «Recently, a Ferrari 250 GTO of 1962 was auctioned for the record figure of 48,405,000 dollars. Then, they are vehicles not affected by devaluation but, contrary to normal supercars, they gain higher value as soon as the leave the dealer».
What are the main pluses for an electrified hypercar?
Primarily, the maximum torque at zero revolutions granted by the electric propulsion that allows immediacy in the response to the impulses of the accelerator and not losing time in gear changes. I add that the centre of gravity is positioned lower than in an endothermic vehicle for the favourable positioning of the battery, with remarkable advantages linked with load transfers; this improves the longitudinal performances, then acceleration and braking. Electric hypercars are often provided with four independent motors, therefore it is possible to deliver adequate torque to each wheel and to exploit the adhesion limit of the tire, optimizing its traction qualities. The use of electronic differentials in a vehicle with endothermic motor does not allow a so efficacious control.
What are instead, still today, the most critical aspects?
Mainly the weight that is strictly connected with the energy density of the battery. Today it reaches about 250 wh/kg, still not sufficient to be competitive in terms of revolution performances with an endothermic vehicle. Having two independent motors on the same axle means to have to emulate a traditional differential but with licit perplexities concerning safety: a wrong signal to one of the two motors while the vehicle is engaged in a curve can have disastrous consequences. Therefore, huge efforts are necessary in this ambit, to optimize performances and safety. If a great quality of an electric motor is the easy development of a high instantaneous power, the delivery continuity represents a critical element. Rimac hypercar, for instance, declares powers approaching 1500 kW, probably it succeeds in maintaining them just for few seconds and only under certain conditions of external temperature and battery charge. The endothermic motor, on the contrary, grants the same performance for a prolonged time, with the exception of modest variations depending on environmental conditions like temperature, pressure and relative humidity. The challenge consists in managing the cooling so that temperatures remain as slow as possible; one of the main dangers is precisely the heat released by electric components and this limit compels to declass significantly the torque delivered to wheels when you pursue the highest performances. Creating a high-performance electric vehicle is a committing, but at the same time exciting, challenge because it deals with consolidated technologies, refined in dozens of years. Certainly, the endothermic vehicle starts in advantage but we are quickly recovering».
What is the next frontier?
Operation voltages exceeding 1000V and batteries at the solid state. We will see incredible things…
What is your favourite hypercar?
It is the fully electric hypercar that we would like to develop here, in our technical centre, and we hope we will soon have the opportunity. We work at research and development for most of our time and it is part of our job to recognize as passable those barriers that others deem unsurmountable.
*AVL is an Austrian multinational and in Italy it has a futuristic technological hub at Cavriago, in Reggio Emilia province. The company’s activity consists in research and development on advanced powertrain systems, from traditional internal combustion engines up to purely electric motors and encompassing the revolutionary fuel cells. The ITS division of AVL works at the design and manufacturing of test benches for the test and the validation of traction systems.
Impregnating resins for mechanical stability and insulation
Axalta’s bespoke automotive products provide electrical insulation solutions and are designed to improve the performance levels of modern electric motors. They include Voltron wire enamel, Voltatex 4200 for impregnation, and adhesive electrical steel coatings such as Voltatex 1175W and Voltatex 1075K. Axalta has been a global supplier in the manufacture of high-quality, high-performance liquid insulating systems and materials for over 70 years and it supplies its Energy Solutions range of Impregnating Resins, which provide mechanical stability and insulation for electrical motors in full electric as well as hybrid vehicles, to nearly all well-known light vehicle OEMs. Michael Glomp, Vice President of Axalta’s global Energy Solutions business, says, “The development of efficient, high-performance and reliable engines for hybrid and electric vehicles continually presents new requirements and challenges for electrical insulation materials.”
Expanded systems simulation capabilities
This latest release of Ansys Pervasive Engineering Simulation solutions empowers more users to accelerate the design process with its new single window, efficient workflows and patent-pending advanced meshing technology for computational fluid dynamics (Cfd). Users will greatly benefit from new processes for developing embedded software for safety-critical applications, dramatic computational speed and user experience improvements.
The Ansys systems suite has new features and functionalities that are essential for the development of digital twins, autonomous and electric vehicles. New capabilities in make it easier and faster to build, validate and deploy digital twins. Now users can visualize 3D fields of static Roms and view simulation results, like velocity and flow rate, on the 3D geometry.
With the recent acquisition of Optis, Ansys is introducing Ansys Vrxperience. This new solution takes predictive validation of vehicle systems to the next level – meeting any virtual reality simulation and validation need for autonomous vehicle simulation, including complex systems such as intelligent headlamps, interior and exterior lighting, autonomous vehicles controls and HMI validation. Vrxperience also enables users to fully and realistically simulate autonomous vehicles using real-world conditions, including various weather and road conditions, oncoming vehicles, pedestrian scenarios and anticipating the vehicle’s reaction to any critical situation.
Motors and drives
Drives constitute an essential part of the manufacturing sector because they are the real “muscles” of CNC machines. in this article the main typologies available on the market are analysed.
The drive is a suitable system for performing a linear or rotary motion and includes both the motor and its control system. It is possible to classify them according to the three main application fields:
- Drives for the spindle rotation;
- Drives for x,y, z linear axes;
- Drives for circular axes
Historically, concerning the spindle, they used systems with motion transfer to belt and gears: the latter allowed achieving a transmission whereas the belt reduced vibrations. Such system assured high power and torque values but low speed values. The motion transmission could occur also through a coupling: this represented a “safety” aspect for the machine tool because, in case of anomalies, it broke down without damaging the machine. In comparison with the first case analysed, the motion transmission through coupling assured higher speeds to the detriment of powers. Precisely the electrospindle has allowed finding the right compromise in terms of speed and power (that is to say, integrated motor and spindle). This has also enabled to obtain more compactness and lower vibrations.
Motors integrated into the spindle
Until 2000, DC motors were used but with the advent of technology and a substantial improvement of power electronics (more and more powerful microprocessors and development of inverters), it was possible to introduce AC ones. Direct current motors allow a precise regulation of torque and nominal power. However, they are scarcely sturdy and rather expensive, besides needing a quite ordinary maintenance of the collector and of brushes. Moreover, they are cumbersome motors (in general, speed increases hand in hand with sizes). As time went by, alternating current motors were developed. The have discretely adjustable speed through a speed gear but they also strongly depend on frequency, as indicated in the following formula:
n = 60 * f/p
where:
n= rotation speed (rpm)
f= net frequency
p=number of polar torque
A noteworthy novelty was the introduction of the inverter that, in alternating current motors, has allowed varying the net frequency, permitting to increase the variability range of the motor speed. AC motors are very reliable, simple and highly performing. In CNC machines is broadly used the so-called electrospindle, a very compact and stiff system, which allows achieving high torque and speed.

Motor of linear axes
To move the linear axes of the machine tool, rotary motors are almost always used and therefore it is necessary to combine a system that transforms motion from rotary to translating. The motion transformation system is composed by a system with re-circulating ball screw in case of CNC machines and by a screw-nut screw system in case of a conventional machine. In general, the characteristics demanded to a motor for linear axes are the following, as listed below:
- Each axis must be equipped with an independent drive;
- Motors must be compact;
- They must permit progressive speed variations;
- They must have very high rapid feed speeds to reduce transients as much as possible;
- High pickup and braking currents;
- High accelerations.
Among the solutions most adopted, it is worth highlighting:
- DC servomotor with permanent magnets. Generally, the DC motor that powers the spindle is equipped with windings on both the stator and on the rotor and therefore they are independent excitation motors. In the motor for linear axes, the windings on the stator are instead replaced with permanent magnets. Windings are mounted on the rotor and they receive electric current from brushes. The latter, however, are subjected to wear and, for that reason, they need periodic maintenance. To avoid that, “brushless” servomotors are used, in other words without brushes and with magnet on the rotor and winding on the stator part. In this way, motors become even more compact but the problem of the rotary magnetic field management emerges. Therefore, powering the winding on the stator in controlled manner becomes necessary, in order to minimize torque and speed oscillations. Hall-effect sensors are used, as they can manage the switchover of the winding on the stator as they detect the magnetic field generated by the rotor and its relative position as to the rotor. Concerning the switchover, it generates some torque instabilities called, precisely, torque ripples. The main advantages of a brushless motor, in comparison with a standard DC motor with permanent magnets, are the following:
- Higher rotation speed;
- Low inertias;
- Inferior nominal torque to the DC one but with a maintenance of the torque itself for a much longer time;
- Higher efficiencies;
- Smaller overall dimensions;
- Low maintenance.
2. Stepper motor. It is a synchronous motor where the rotation speed is varied by changing the frequency of control pulses. The operation is very simple: whenever the motor detects a pulse, it rotates by a certain angle. The torque in this case is not constant but it rapidly decreases as the speed rises. It is a very precise motor and therefore it grants certain result sureness. Sizes are very small.
Motors for rotary tables
Recently, they have developed linear motors that allow solving the problem of the motion transformation from rotary to linear, because approximate 15% losses occurred with the motor transformation. The linear motor is a real “linearization” of the brushless motor. It is worth noticing that the motor is as long as the axis to be driven. Therefore, magnets must be perfectly aligned. Then, we refer to:
- Long inductor, when magnets are positioned on the fixed part;
- Short inductor, when magnets are positioned on the mobile part.
- Among the advantages, we are pointing out:
- High speeds;
- High accelerations;
- High precisions;
- High stiffness.
Nevertheless, they are affected by some relevant limits, like:
- Low efficiencies;
- A bit complex heat disposal;
- High costs;
- Redesign of the machine tool.
Electrospindles and energy saving
The paradigm of energy efficiency increase, branded industry 4.0, is accomplished also through the definition of spindle solutions oriented to energy saving: new scenarios at the horizon for machine tool manufacturers, which behold opportunities connected with the eco-design of the spindle subgroup and the advent of innovative direct-drive solutions.
Manufacturing represents one of the industrial sectors characterized by a high energy demand: for this reason, national and European institutions, universities, industrial associations, regulatory bodies and companies have started – at different levels and each with its own role – introducing policies, directives and solutions oriented to increase the sector efficiency. Various studies and works carried out on stock removal machine tools have highlighted how a potential energy saving can be achieved through opportune design choices aimed at the use of more efficient technologies and components and at a better machine use in terms of definition of operating parameters and/or machining strategy. In the specific case, the present article focuses on the aspects of efficiency and energy consumptions of the spindle systems that equip CNC machining centres. The current developments referred to the spindle/electrospindle ambit are mainly aimed at the enhancement of static, dynamic (stability, vibrations, chatter, removal capacity and so on) and productive performances of such machine elements, however paying growing attention to “eco” and energy consumption aspects. It is in fact worth underlining that the spindle, together with the relative auxiliary systems, constitutes one of the main energy-eater machine components in use phase, during the execution of machining processes for the manufacturing of finished products.
Spindle system and operating conditions
Spindles are rotary elements generally designed and manufactured for a broad array of machine tools used in several application sectors (aerospace, automotive, etc.) with the general target of maximising the stock removal rate and accuracy, consistently with the existing constraints. Since NC machining centres generally need to execute several machining operations on the same workpiece, the spindle system must be suitably designed for assuring the demanded flexibility level and the desired performances (speed, torque, power and accuracy) within the wide range of admissible operational conditions.
Electrospindles and efficiency maps
Let us consider, as an example, a machining centre for milling operations: a relevant percentage of the energy consumption is connected with the spindle, depending on the torque and rotation speed demanded by the process. If an electrospindle is used, it is fundamental to consider also the consumption of the chiller that cools motor windings: the coolant circulation pump determines an important contribution to the “basal consumption” (independent from the various activities executed by the machine). In this case, the efficiency of the spindle + chiller subsystem can be defined as ratio between the output mechanical power from the spindle (towards the process) and the overall electric power absorbed by spindle and chiller, which is function of the demanded load. Such efficiency can be assessed experimentally through power measurements carried out by subjecting the spindle to different combinations of torque and speed, thus achieving a mapping. Then, it is possible to distinguish:
- acceleration/deceleration phases related to the spindle start and stop (that actually use the whole available power)
- longitudinal turning machining (at constant speed)
- parting off/facing machining (at growing speed, with the decreasing radius)
The brushless motor used would reach 95% of efficiency close to the high-torque region and lower speeds than defluxion one. The chiller action damages low-torque “zones”: since the majority of the test cycle examined occurs in regions with efficiency in the 20-70% range, the overall efficiency produced is much lower than the theoretical maximum. Hence, we therefore infer an indication for machine tool manufacturers: in designing a machine, it is important to evaluate the spindle system efficiency (with the eventual addition of the chiller and other auxiliaries) compared to the real requirements of the user regarding the machining cycles to be executed, in terms of speed and torque to be delivered. Moreover, it is desirable that the regulation activity concerning the evaluation of the environmental impact of machine tools – promoted by ISO WG12 and, on a national scale, by the relative UNI work group –can lead to standards for the definition of tests of “machine-based” energy measurements, aimed at a characterization, even simplified, of such efficiency maps: the goal is prescribing the execution of measurements that “sample” the efficiency in some reference points.
Expanded systems simulation capabilities
This latest release of Ansys Pervasive Engineering Simulation solutions empowers more users to accelerate the design process with its new single window, efficient workflows and patent-pending advanced meshing technology for computational fluid dynamics (Cfd). Users will greatly benefit from new processes for developing embedded software for safety-critical applications, dramatic computational speed and user experience improvements.
The Ansys systems suite has new features and functionalities that are essential for the development of digital twins, autonomous and electric vehicles.
New capabilities in make it easier and faster to build, validate and deploy digital twins. Now users can visualize 3D fields of static Roms and view simulation results, like velocity and flow rate, on the 3D geometry.
With the recent acquisition of Optis, Ansys is introducing Ansys Vrxperience. This new solution takes predictive validation of vehicle systems to the next level – meeting any virtual reality simulation and validation need for autonomous vehicle simulation, including complex systems such as intelligent headlamps, interior and exterior lighting, autonomous vehicles controls and HMI validation. Vrxperience also enables users to fully and realistically simulate autonomous vehicles using real-world conditions, including various weather and road conditions, oncoming vehicles, pedestrian scenarios and anticipating the vehicle’s reaction to any critical situation.
Testing e-trucks in Europe?
Waberer’s (vehicle operator in international full truckload transportation in Europe) is willing to test and is open to participate in the introduction of Tesla’s e-trucks in Europe.
Also, as the firsts from Europe, Waberer’s tested the Tesla Semi e-truck designed for long-distance transportation.
Waberer’s and Paccar Group (supplier of Daf trucks) are discussing the testing and introduction of electric and driverless vehicles under development.
“We at Waberer’s are committed to continuous innovation and seize every opportunity participate in our partners’ R&D and innovation programs. Electric and driverless truck developments may significantly reduce the environmental impact of road transportation and have a favourable effect on the cost side at the same time. We see a great opportunity in developments concerning logistic infrastructure. In fact, we have effectively implemented several digital innovations in our operations”, said Ferenc Lajkó, Ceo of Waberer’s.
Engineering e-motors
When car manufacturer Daimler formed a joint company in 2011 with Bosch, the world’s leading automotive supplier, the synergy between the two companies was obvious.
The joint company, EM-motive GmbH, combines Daimler’s expertise in fuel cells and batteries with Bosch’s knowledge of the development and production of electric motors to design and manufacture electric traction motors for electric and hybrid vehicles.
Because the motors are designed to be modular, they can be adapted to fit a variety of vehicle classes and meet specifications for many different vehicles.
Since 2012, the company has manufactured more than 300,000 e-motors for client companies throughout Europe.
Even with this combined expertise, manufacturing a modular engine is complex and challenging. In addition to the main engineering constraints (cost, mounting space for the motor, cooling and inverter-specific properties), the customer-based requirements for each type of engine cover a wide breadth of individual physical domains:
-Thermodynamics: coolant flow rate and temperature, environmental temperatures, as well as winding and magnetic temperatures
-Structural mechanics: mounting space, torque, power, speed, tolerances to other parts and forces on bearings
-Electrical engineering: voltage, current, inverter-specific properties
-Efficiency and acoustics: airborne and structure-borne noise
To make the challenge even greater, all of the parameters to be optimized have to be considered simultaneously. Other factors must also be taken into account: noise, vibration and harshness (NVH); safety; and the cost of the engine.
The engineers at EM-motive realized that, in such an interactive environment, a “classic” component development system, where rigid specifications for each component are designed separately and then assembled, was no longer possible.
Instead, the company developed a design workflow that incorporated simulation throughout to account for the dynamic interactions between the components, as well as all the necessary parameters to determine optimal solutions and ensure design robustness. The parametric workflow to support sensitivity analysis, design optimization and design robustness evaluation includes ANSYS simulation software and other software tools, and was built and hosted in ANSYS optiSLang.
These workflows help EM-motive to develop electric motors within challenging time and cost requirements, as well as resolve customized design challenges, such as a late-stage customer requirement change for an engine design.
As an example, a customer requested that the maximum speed for a particular engine needed to be increased by 1,000 revolutions per minute (rpm). The centrifugal forces of the accelerated speed, however, would cause the rotor design to fail.
The engineers could increase the bridge thickness of the pockets for the magnets that are punched into the rotor lamination to withstand stress caused by the higher centrifugal forces. However, this would increase the flux leakage in the rotor itself, causing reduced torque and power.
An option to address this reduction is to increase the current in the windings (but only if higher current is available from the battery and electronics system).
This solution would intensify losses and reduce efficiency, and was not acceptable to the customer. It was therefore necessary to redesign the entire engine to comply with all requirements.
Fortunately, the EM-motive simulation workflow can be flexibly adapted to analyze the requirements for a specific engine, simulate all the dynamic interactions between the components, and present the customer with a solid understanding of the trade-offs for each design decision.
The workflow provides the foundation to determine the best compromise for often contradictory goals.
A workflow for digital exploration
During the procurement phase, using ANSYS optiSLang workflow connected to CAD and employing specialized electromagnetic–thermal software, the design engineers have the freedom to explore possible variations and their tolerances to fulfill customer requirements. They can then provide a fast answer so the customer will know if the requirements can be met with available motors or if new motor development is needed.
Through a set of iterative phases in which additional requirements are added, a new motor is designed and optimized using ANSYS simulation software in all the relevant physical domains. A shared interface with the ANSYS Simplorer systems simulator helps them analyze the influence of power electronics on the motor.
Because there is a bidirectional interface between ANSYS DesignModeler and the CAD system, engineers can create parameterized models of auxiliary geometries, such as the housing, and integrate them into the system design. The ANSYS tools allow the designers to use the results of one type of simulation as a boundary condition for another.
They can then use forces from an electromagnetic simulation with ANSYS Maxwell as initial data for a structural mechanical simulation with ANSYS Mechanical.Using the various ANSYS tools integrated through ANSYS Workbench makes it possible to create a completely coupled simulation of the electromagnetic, mechanical, thermodynamic and acoustic domains.
With these parametric workflows in place, all important physical domain sensitivity studies within the relevant design space, as well as tolerance determination, can be conducted.
The engineers can add further optimization loops, but because of the conflicting character of many discipline goals and constraints, and because of the need to quickly check the motor behavior on a systems-simulation level, reduced-order models (ROMs) must be extracted. Using the integrated equivalent circuit extraction (ECE) toolkit within ANSYS Maxwell or ANSYS optiSLang’s data-based ROM generation, the team can extract reduced models for an overall system simulation.
Systems modeling
These reduced-order models can be coupled in ANSYS Simplorer to create a complete system simulation. Again a parametric workflow is built within optiSLang and, optionally, other third-party models can be integrated, such as a transmission model or a complete vehicle model. At this point, the engineers might perform a system optimization loop to analyze the interactions between the components by varying parameters such as those for the controller.
Finally, to make the model interchangeable with additional engine components designed by outside parties, the designers use the industry-standard functional mock-up interface (FMI) to create models of the individual components, called functional mock-up units (FMUs). These FMUs are created with third-party software and can easily be exchanged while maintaining IP confidentiality: since they contain only standardized inputs and outputs, the product-specific know-how is only accessible to the manufacturer.Another advantage of FMUs is that they can be imported into all current software packages for system simulation and can describe, for example, the behavior of the e-machine as a single component in the simulation landscape of a customer or development partner.
Understanding the options
The final challenge is to present the optimized designs so that the customer can clearly understand the different design choices and their trade-offs. EM-motive developed a single radar diagram that transforms all performance indicators into dimensionless variables using the requirements as standardization values.
It includes all domains and their requirements, further highlighted with a colored pie chart in the background, to clearly represent the domains.
All points that are located outside of the 100 percent reference circle meet the design requirements.
Interactions between physical domains are also easily depicted in the diagram. If, for example, a design should be revised to improve acoustics, the mostly negative effects on efficiency are plainly shown.
The chart provides a comprehensive understanding of the strengths and weakness of each redesign and how it fulfills (or doesn’t fulfill) their unique requirements.
Engine design, like many complex processes today, requires a collaborative, systemic approach to be successful.
EM-motive’s systemic approach to engine design integrates the ANSYS parametric simulation environment and an innovative presentation method to ensure that their automotive manufacturing customers can develop the next generation of hybrid and electric vehicles within challenging time and cost constraints.
(Marc Brück, Senior Expert Simulation Technology, EM-motive GmbH, Hildesheim, Germany- This article was originally published on “Ansys Advantage”)