25During the last ten years, the market has requested sometimes to increase the operational flexibility of cooling systems using auxiliary pumps for a better control of engine cooling and efficiency, in order to meet more stringent regulations in terms of CO2 emissions. In many cases the auxiliary pumps are driven by brushless motor, regretfully still with some limited performances in terms of pump efficiency and vibrations/noise failures, as it has been for dishwasher application of this type of motor.
Meccanotecnica Umbra developed a material for sliding parts such as bushings to reduce the sliding friction: the solution had been the MTU Ptfe material with appropriate fillers, Mecflon.
Meflon, when compared to other grades of Ptfe, is formulated to provide increased efficiency, improved wear resistance, and decreased starting torque in demanding applications of food, spa, and drinkable water segments. As it was for the mechanical seal of dishwasher pumps, MTU analyzed the possibility of supplying in particular bushings and rings, made with same innovative materials to prevent sticking and noise, to Tier1s and OEs that are partially replacing the traditional pumps (equipped with mechanical seals).
The irregularities of performances in real conditions are related to the occurrence of irregular flow situations and for mechanical seal, this phenomenon is bigger, because the lubricating film between the faces is typically very small. Therefore, the effect of Mecflon also for bushings has been again the key factor for avoiding sticking and noise, as it had been for traditional low power electric pumps, provided with mechanical seals.
In the past two years MTU has got relevant progress in the definition of the project for brushless motors and has overtaken the preliminary testing activity on prototypes, with sizeable advantage also in terms of wear, and not only sticking and noise, in comparison with standard materials used for mass production.
Pumps equipped with Ptfe bushings don’t present axial wear of the front flange of the bushing and show lower wear of radial surface.
However, the combined radial wear of bushings and shaft for Mecflon Y4 solutions makes significantly lower overall damage in terms of eccentricity.
Morerecently MTU has started a specific development program for application of PTFE bushing to cooling system water pump , taking into account the typical working conditions of the automotive segment (-40/140 ° C, up to 6000 rpm, high additivated coolant, continuous operation during in-house recharge of batteries of hybrid or electric vehicles).
Mecflon to avoid noise and reduce friction an losses
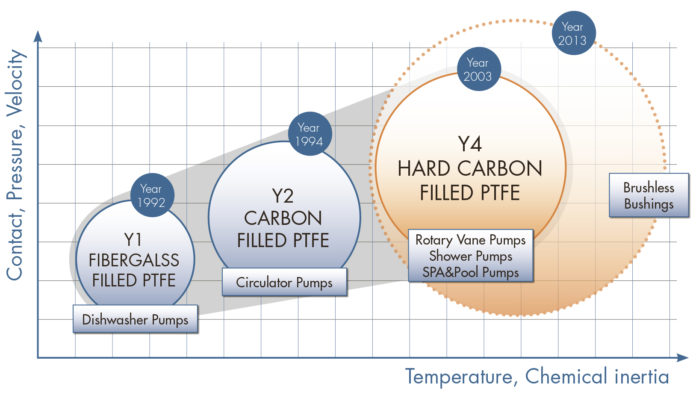
High-efficiency motors and sustainability
According to some studies, electric motors are responsible for about 45% of the total consumption of electric energy [1]. If we focus the analysis on one the most energy-eating ambits, the industrial one, the percentage ascribable to motors rises to around two thirds.
Considering that several of the machines currently in operation are obsolete, it is clear that the replacement with new more efficient motors would lead to important advantages for the environment and the resource exploitation, as well as in manufacturing costs and then in competitiveness. They estimate for instance that, in the only Europe, the use of forefront drive technologies instead of obsolete ones can determine a reduction of yearly consumptions by 135 TWh and CO2 emissions by 69 million tons [2]. Evaluating the entire life cycle of a motor in constant operation, we can verify that the spending connected with the energy consumption represents by far the major percentage in the total cost (even more than 90%, [3]).
For these reasons, in the European Union, as well as in the United States, in China and in other Countries, are in force regulatory plans providing for the mandatory compliance with gradually increasing efficiency requisites for new installations. According to the Minimum Energy Performance Standard (MEPS), for instance, the motors released on the EU market since January 2017 in the power range from 0.75 to 375 kW must have IE3 efficiency level or IE2 efficiency level if powered by inverter (see Fig. 1), with very few exceptions.

With the technology most diffused among motors today, the asynchronous motor one (or Induction Motor, IM), the improvements demanded in the future will not be possible, at least at reasonable costs, and for all power ranges. These aspects, combined with other factors such as the growing awareness of the importance of decreasing energy consumptions, are leading to the adoption of motors scarcely spread until now, such as Permanent Magnet Synchronous Motors, [4][5]. This class of motors, in fact, features intrinsic characteristics that allow a notable improvement of the efficiency and of the power density, in particular very low rotor losses.
Even if already in the Eighties “brushless” servomotors (i.e. Surface Mount‑PMSM, SM‑PMSM) have been used in industrial automation, thanks to their excellent controllability and high dynamics, the application of electric synchronous machines with unwound rotor has remained limited to particular applications for a long time. Over the last few years, on the contrary, thanks to the above-mentioned factors concerning efficiency and the decrease of production costs of motors and inverters, the adoption of this type of motors is notably spreading.
Classification of AC motors
The majority of alternate current (AC) motors is three-phase, even if there are some exceptions like in the case of single-phase and stepping motors (that are generally two-phase). The most important distinction is generally between synchronous and asynchronous machines, difference based on the fact that the mechanical rotation speed, at steady state, is strictly connected (synchrony) or not with the rotation frequency of the stator magnetic field. This difference is concretely mirrored in the fact that, to generate torque in the asynchronous machine, the presence of induced currents in the rotor is necessary, whereas it is not needed (and, on the contrary, undesired) in synchronous machines.
Synchronous machines are characterized by the fact that the magnetic rotor field is geometrically bound to the mechanical position of the rotor itself. The rotor field can be generated by a current that runs through a winding (synchronous motors with wound rotor), by permanent magnets (permanent magnet synchronous) or by the stator current itself, modulated by the magnetic anisotropy of the rotor (synchronous reluctance).
Structurally, both the rotor and the stator of radial flow machines (that are by far the majority) are manufactured by stacking ferromagnetic laminations opportunely blanked, solution aimed at hindering the parasite currents. The rotor is generally cylindrical and can be equipped with spaces to house permanent magnets or conductive material.
In Fig. 2 are schematized the sections of the various types of motors just listed (with the exception of the synchronous one with wound rotor).

The darkest areas (slots) correspond to windings, permanent magnets are indicated in blue whereas the grey zone of the section represents the ferromagnetic material (lamination). As you can see, the difference among the various motor types is concentrated in the rotor, whereas the stator (unless particular cases) can be implemented in the same way. In the asynchronous motor, the rotor slots are filled by a fusion, which constitutes the so-called “squirrel cage”, generally made of aluminium or, recently, of copper (with higher costs, in order to reduce losses).
In permanent magnet motors, instead, magnets can be introduced into apposite carvings inside the rotor structure (IPMSM and line-start IPMSM) or applied on the surface in case of SM‑PMSM. In the SynRM case, instead, the carvings inside the rotor are simply void and called “flow barriers”, since they perform the function of increasing the reluctance (i.e. the capability of opposing the magnetic flow passage) along some directions, favouring instead others (i.e. the paths more characterized by the presence of iron).
In their turn, synchronous motors can be subdivided according to the torque production principle. In surface permanent magnet motors, the torque production occurs only thanks to the interaction between the field generated by permanent magnets and the stator current.
Vice versa, in reluctance motors, it is exploited the system tendency to minimize the reluctance of magnetic paths, if subjected to excitation. In internal magnet motors (IPMSM), both principles are generally exploited.
In the production of permanent magnets, particular materials are used, to achieve high induction values and to prevent the risk of demagnetization (generally linked with high temperatures or high magnetic field). The most used materials are neodymium -iron-boron, samarium -cobalt and aluminium-nickel-cobalt. Especially in the SM‑PMSM case, the quantity of active magnetic material is high, with a strong weight of raw materials in the total cost. This condition is worsened by the strong variability of the price of the so-called “rare earths” [7], elements used in small quantities but very important for the magnet quality. Apart from cost and availability problems, these materials arouse also important environmental, political and ethical issues regarding their extraction, trade and disposal. For these reasons, huge resources are invested in the research and development of different materials and, especially, in the project of motors that minimize the use of permanent magnets, [8], or that allow the use of the so-called ferrites, i.e. ceramic magnetic materials that use less problematic materials.
Power supply through inverter and control
A negative aspect of synchronous motors derives from the impossibility of powering them simply connecting them with the net (Direct On‑Line, DOL), as it instead occurs for asynchronous ones. For the operation of permanent magnet synchronous or reluctance motors, the presence of a “drive” is therefore necessary, i.e. the whole consisting of the real inverter (a pure electronic power actuator), of the electronic controller and the algorithms implemented in it. The control algorithm, implemented on a digital device, is updated with frequencies in the order of 10,000 times per second. Despite the additional cost, it is worth considering the possibility of varying the operation conditions, in particular speed, brings important advantages in several applications (especially pumps and fans, where it allows notable energy savings).
Controlling the inverter in PWM (Pulse Width Modulation) it is possible to generate efficiently a tern of voltages that are characterized by amplitude, frequency and arbitrary phases.
Since in synchronous motors the torque depends on the current amplitude and on its phase relation with the magnetic axis of the rotor, in control algorithms the Park coordinate transformation is generally used, thus bringing the three-phase system to a reference system integral with the rotor axis (Fig. 6).

The knowledge of the rotor position is then essential for the synchronous motor control. In some applications, where no particular control performances are required, it is possible to eliminate the mechanical position sensor, owing to the cost and the reliability decrease stemming from it. “Sensorless” control techniques have in fact been developed, where the rotor position is estimated exploiting current and voltage measurements (inside the inverter and anyway necessary) and the motor model.
Sensorless techniques for synchronous motors, developed since the Nineties, initially found application in some specific cases only. In the products currently called “inverters”, i.e. those drives for generic use, the first algorithms of this type were introduced in the late 2000s, to become then an almost standard equipment in the last years. Unfortunately, these solutions are still scarcely known by automation operators, even if their validity has been demonstrated, especially in common applications like pumps and fans.
Since the data supplied by the motor manufacturer are often insufficient for the calibration of all parameters of the control algorithm, “self‑commissioning” methods have been developed, in other words commissioning with the operator’s minimum intervention. The first step is the automatic identification of parameters (“self‑identification”), with methods fulfilled by the drive itself, to proceed then to the real calibration, i.e. the choice of the values for control parameters. Both industry and the academic world actively research on these aspects, with very interesting proposals also in Italian ambit, [10]-[14].
Structural details
As already said, the biggest difference among the various types of AC motors mainly resides in the rotor structure. There are in fact various cases of synchronous motors designed to keep the other parts almost unchanged compared to a corresponding asynchronous machine (eventually changing the winding turns). This kind of approach has spread in the last few years, with the aim of satisfying generic applications, precisely as substitution of the asynchronous motor. Besides the evident advantages in manufacturing costs, the use of equivalent parts in terms of overall dimensions, supports and external fixing points has allowed adopting these motors without modifying the remaining mechanics. Concerning this, innovative examples are represented by Italian companies’ products, like the series of internal permanent magnet synchronous motors and reluctance motors illustrated in Fig. 5.

In synchronous motors, especially in permanent magnet ones, it is possible to implement a high number of poles, with a speed reduction with the same voltage and a torque increase with the same current. This degree of freedom in the project can be compared, by analogy, to the use of a mechanical speed reducer and therefore, in some applications, it allows using a direct‑drive connection, with some advantages in terms of efficiency, overall dimensions, cost, reliability and control precision. This solution has been adopted for some years in industrial machines (for instance, in the production of paper, [14]), in the civil lifting sector (lifts), in the air treatment (cooling tower fans, [15]) and in some household appliances (in particular washing machines).
In the project considered in [15], the stator pack (laminations) has been used as structural element, without the addition of an external case. Fig. 6 reports also the design of a stator lamination, where is visible the external wing for the heat dissipation. Thanks to the overall dimensions limited in height, this motor is mounted at the base of the cooling tower, in axis with the fan, thus avoiding the right-angled transmission and the speed reduction, which are instead necessary in the traditional configuration (with asynchronous motor).
Applications
The first applications in the civil sector of permanent magnet synchronous motors include conditioning systems, due to the importance that energy consumption holds in that case. In the refrigeration as well (both industrial and domestic), the adoption of synchronous motors has gradually grown. Besides, a particular case is represented by circulation pumps for heating plants that, due to efficiency reasons, nowadays are almost totally based on permanent magnet synchronous motors in sensorless control.
Among household appliances, in washing machines the use of these motor types has become common in the last few years. The use of synchronous motors instead of asynchronous or universal (with brushes) has permitted on one hand the reduction of overall dimensions and of the quantity of used material, on the other hand a better controllability, also linked with the adoption of solutions such as the mechanical direct-drive connection. In the latter case, due to overall dimension constraints and torque requisites, the rotor is usually external and the entire motor is flat and with big diameter (Fig. 7).

A detail of the production of this type of machines, shared also by other particular applications, is the winding on the tooth (a distinct winding for each stator tooth).
In this type, idle copper parts are reduced but it becomes more difficult to design machines with low torque ripple. The direct coupling provides advantages also from the point of view of the overall operation, facilitating the load identification in the tank and its arrangement, in addition to the speed control.
Due to the particular working cycle of washing machines, which includes the spin-drying, the operation at high speed (exceeding the nominal) is important. This modality is called “defluxing”, because, being the voltage proportional to the flow and to the speed, the overall flow is reduced through an opportune control, to allow the operation at higher speeds and fixed voltage. In this case, internal permanent magnet synchronous motors are the main candidates, since their available torque does not drop suddenly beyond the nominal speed.
An ambit where synchronous motors have become highly present are lifts, especially of big size. In this case, too, specific solutions have been implemented, like the one in Fig. 8, allowing the direct load motion (gearless).

In this case, it is an axial-flow motor, i.e. the gap between stator and rotor (magnetic gap) is crossed by field lines that are parallel to the axis.
Other specific application fields concern renewable sources (for instance wind power) and avionics, where they pursue the target of “More Electric Aircraft” (replacement of hydraulic or pneumatic actuators). The use of high-efficiency and high-density motors is also spreading in traction, including the road ambit (from bicycles to heavy vehicles and operating machines), the railway/tramway sector and the industrial one (forklifts and similar).
Bibliography
- Wilde, C. U. Brunner,”Energy-Efficiency Policy Opportunities for Electric Motor-Driven Systems”, International Energy Agency, Working paper, 2011.
- “Electric Motors and Variable Speed Drives – Standards and legal requirements for the energy efficiency of low-voltage three-phase motors”, ZVEI – Zentralverband Elektrotechnik- und Elektronikindustrie e.V., Division Automation – Electric Drive Systems, Frankfurt, December 2010, 2nd Edition.
- “Boosting industrial profitability with energy efficient drives and motors”, ABB brochure, 2016
- Vagati, “The synchronous reluctance solution: a new alternative in AC drives,” 20th International Conference on Industrial Electronics, Control and Instrumentation, 1994. IECON ’94., Bologna, 1994, pp. 1-13 vol.1.
- Lipo, T. A., “Synchronous reluctance machines – a viable alternative for AC drives.”, Wisconsin Electric Machines and Power Electronics Consortium, Research report, 1991.
- “Low voltage Process performance motors according to EU MEPS”, ABB catalog, October 2014
- “Rare Earths”, S. Geological Survey, Mineral Commodity Summaries, January 2016.
- Guglielmi, B. Boazzo, E. Armando, G. Pellegrino and A. Vagati, “Magnet minimization in IPM-PMASR motor design for wide speed range application,” 2011 IEEE Energy Conversion Congress and Exposition, Phoenix, AZ, 2011, pp. 4201-4207.
- “Motor technologies for higher efficiency in applications – An overview of trends and applications”, Danfoss Power Electronics – Danfoss VLT drives PE-MSMBM, November 2014.
- N. Bedetti, S. Calligaro; R. Petrella, “Stand-Still Self-Identification of Flux Characteristics for Synchronous Reluctance Machines Using Novel Saturation Approximating Function and Multiple Linear Regression,” in IEEE Transactions on Industry Applications, vol. 52, no. 4, pp. 3083-3092, July-Aug. 2016.
- N. Bedetti, S. Calligaro; R. Petrella, “Self-commissioning of inverter dead-time compensation by multiple linear regression based on a physical model,” in 2014 IEEE Energy Conversion Congress and Exposition (ECCE), vol., no., pp.242-249, 14-18 Sept. 2014.
- N. Bedetti, S. Calligaro; R. Petrella, “Analytical design of flux-weakening voltage regulation loop in IPMSM drives,” in 2015 IEEE Energy Conversion Congress and Exposition (ECCE), vol., no., pp.6145-6152, 20-24 Sept. 2015.
- N. Bedetti, S. Calligaro; R. Petrella, “Design Issues and Estimation Errors Analysis of Back-EMF-Based Position and Speed Observer for SPM Synchronous Motors,” in IEEE Journal of Emerging and Selected Topics in Power Electronics, vol.2, no.2, pp.159-170, June 2014.
- S.A. Odhano, P. Giangrande, R. I. Bojoi and C. Gerada, “Self-Commissioning of Interior Permanent- Magnet Synchronous Motor Drives With High-Frequency Current Injection,” in IEEE Transactions on Industry Applications, vol. 50, no. 5, pp. 3295-3303, Sept.-Oct. 2014.
- Welin, C.-J. Friman, “New Direct Drive system opens a new era for paper machines”, Paper and Timber, Vol.83/No. 5, 2001.
- McElveen, K. Lyles, B. Martin and W. Wasserman, “Reliability of Cooling Tower Drives: Improving Efficiency with New Motor Technology,” in IEEE Industry Applications Magazine, vol. 18, no. 6, pp. 12-19, Nov.-Dec. 2012.
Ferrite transformers for high frequency use
Operative in the winding sector for 40 years, Albe has distinguished itself for the quality of its products and its flexibility in satisfying the requirements of its clients, guaranteeing Made in Italy quality.
The experience gained over the years, combined with modern, cutting-edge equipment, allows the company to offer the best solutions and the most advantageous conditions.
The range of components in ferrite, designed horizontally, vertically, open or resined, is available in all forms (RM-EP-OLLA-ETD-ER-EC-EF-U) and for various uses: filters, transformers, elevators, pulse transformers; and responds to the various requirements of every single type of electronic circuit.
Albe is an Italian company based in Cassano D’Adda (MI) and it makes products according to client specifications: open coils with or without ferrite, pillars on ferrite, sensor coils, relays, electromagnets, laminated transformers up to 20 kVA with CE, UL, Kema and Enec branding. Low profile transformers, ferrite transformers produced in all existing forms. Toroidal filters for low and high frequencies. Compensated and encapsulated toroidal coils, TA. Special Toroids, also wound with multiple wires.
Safety and efficiency in manufacturing automation
Cosberg designs and manufactures plants to automate the mounting systems for all types of electric motors, such as for instance brushless, AC, DC and stepper, intended for several sectors, among which stands out the Automotive. An ambit where, even more than in others, efficiency and safety are essential issues.
For this reason, Cosberg can integrate all available technologies to carry out tests, measurements and controls into the plants, designed and manufactured by the Italian company: dimensional vision controls, component presence, positioning, automated contacting and related electric and tin welding, controlled dosing for the sealing bicomponent, tightness or insulation tests, checks of the noise level, electric tests and so on.
Control and traceability are nowadays irremissible conditions because they allow filing the “story” of each single part and, if necessary, tracing back all underwent machining operations. Therefore, on one hand Cosberg machines assure – and can prove – that each single product has been assembled in full compliance with all specifications provided for by the manufacturer; on the other hand, they must provide each workpiece with its own “package” of information, transmitting all detected data to manufacturers and thus allowing them to monitor, to prevent, to improve and to process statistics. Customers can define what kinds of controls to perform for each production and decide that each single product is labelled and monitored for the entire lifecycle, managing to store all information types: what processes it underwent (and when), on what car it was mounted, what parameters have characterized its production and the values obtained from trials and eventual testing.
Flexibility is another very important aspect for the plants devised for this sector. In fact, for both high-end and “standard” products, there are always countless variables that give birth to endless models and variants. This has led Cosberg, in time, to study solutions offering high reconfigurability levels and drastically reduced set-up times, to meet the ever-rising trend of customizing all aspects of cars and motorbikes. Concerning this, the concept of Lean Production plays a fundamental role, as aimed at the waste reduction and focused on quality, pursuing perfection through constant improvements. Workflows are precisely engineered according to this vision, simplifying the entire manufacturing cycle and eliminating the activities that do not generate added-value, in order to make our systems more and more efficient and flexible.
Cosberg always accepts the challenge for both aspects, traceability and flexibility, because Cosberg must work in synergy at mechanics, electronics and software to satisfy Customers’ expectations. A factor shared by both ambits is precisely the need of controlling and objectifying each operation, in order to eliminate human errors, to avoid wastes of time and resources and to supply “measurable” quality products.
Cosberg can manage all available market technologies that allow reaching these results, like for instance vision and measuring systems, linear and pressure transducers, system management software. Unavoidably, the latter must be faster and faster in filing and processing and, meanwhile, increasingly reliable and safe, as well as – not secondary characteristic – of immediate interpretation and use.
All that allows Cosberg to provide effective solutions to the scenarios that are emerging on the market – where the demand for smaller and customized batches is spreading – and in the advanced manufacturing industry, where production plants are consequently becoming increasingly adaptive, self-configurable and integrated into the manufacturing chain. In other words, Cosberg can state that its plants have already undertaken that evolutionary course that will lead, unavoidably, to that model of Factory that – rightly – Cosberg can define Intelligent.
Hairpin technology for automated assembling
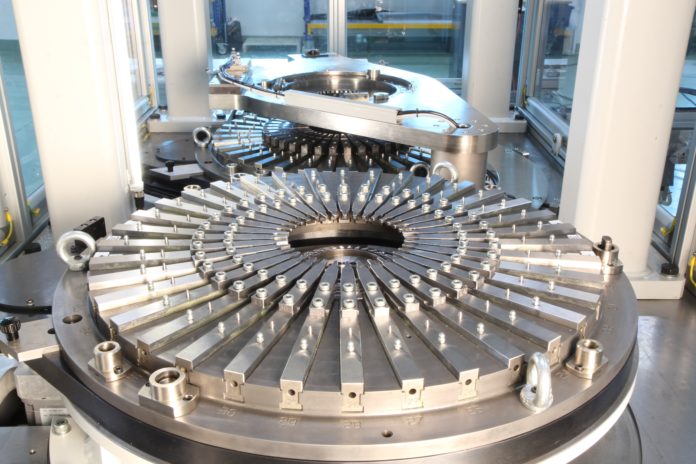
In 2016, around 800,000 electric cars were sold in the world, with the 40% rise compared to the previous year. As many as 63% of them are BEV (Battery Electric Vehicle), i.e. cars whose propulsion is directly supplied by an electric motor powered by batteries.
A more and more significant prevalence that is constantly growing; within 2020, the offer of this vehicle typology on the European market is expected almost to triple, rising from the 20 currently available models to the foreseen 54.
According to the data provided by the E-Mobility Report study carried out by Energy & Strategy Group of Milan Polytechnics in 2016, it is also evident that the world market of the electric mobility is scoring impressive growth rates. To be competitive in this market it is important to bet on the technological innovation of electric-traction motors, which must be increasingly compact, lighter, with higher performances and low consumptions. Atop is specialized in supporting customers in each project phase, backing them in the achievement of this important target.

First, the company executes an analysis of the customer’s product, which needs an engineering assessment aimed at the motor industrialization. Afterwards, it implements the prototypes that allow testing the manufacturing feasibility. Once approved the project and tested its efficiency, Atop produces the machines for the automated assembling of electric motors with hairpin technology, offering the suitable automation level for the demanded productivity.
Flexibility and performances for prototypes and small batches
The special winding hairpin technology, already integrated by Atop in fully automated lines for the production of electric motors for starter and electric- and hybrid-traction motor applications, has been further developed.
The result of the technological progress achieved allows the implementation of very flexible machines, suitable for both the development of prototypes and the mass-production with low production volumes.
The flexibility of Atop machines allows customers to produce hairpin stators with variable shapes and sizes, manufacturing with the same plant motors with different technical specifications.
The machines perform the processes of slot insulation, hairpin forming and insertion, enlargement and twisting, cutting, repositioning and laser welding of terminal wires.
Each operation is carried out with utmost precision and speed, granting an optimal control of every phase of the manufacturing process. The machines implemented by Atop grant the highest flexibility, reliability and user friendliness, exploiting as strong point the capability of offering customized solutions, aimed at satisfying customers’ specific demands, even the most complex, worldwide.
A new technology implementing electric head commutators
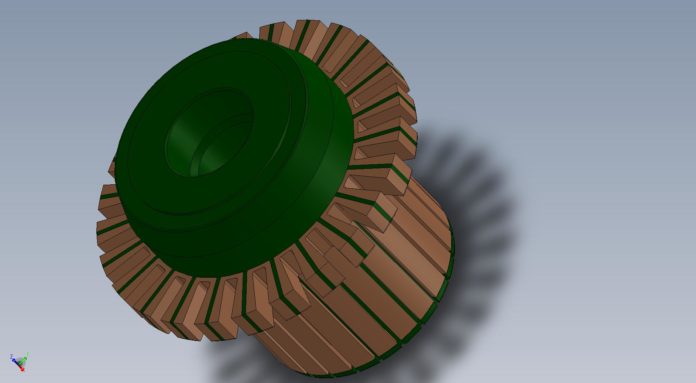
Reference partner in the production of hook-type electric commutators for A.C. and D.C. motors, Cagnoni operates on the market with a very broad range of products (diameters starting from 15 up to 30 mm), suitable for small appliances, automatic door-opening systems, automotive, power-tools, and so on. Such products are implemented starting from a continuous element (copper tube of 5 m) exploiting a unique up-to-date technology, which provides for obtaining the internal grips of the commutator bars from that part of semi-finished product that would be then removed by the successive milling phase.
In that way, no copper is added to create the gripping itself.
That process, developed by Osimo (AN) company itself, will enable a minor waste of raw materials, without affecting the product quality and granting total reliability and extreme flexibility to its customers.
Concerning the sector of electric head commutators, the last decade has been characterized by more and more articulated and interacting competitive factors, summarized in the following points: reduction of sale prices, decrease of component costs, rise of the contents and of the performances of electric motors, increase of the reliability and duration demands.
The offer excess compared to the demand, together with the appearance of unbranded products on the market and, especially, of big low cost producers, have determined a price fall and a standardization “towards the middle” of the functional characteristics of products. In this context, the sector companies’ challenge consists in enhancing the quality and the variety of the offered services by seizing, for instance, the potentialities made available by new technologies.
Increase performances and tear the costs down
The primary manufacturers of electric head commutators use a consolidated technology that provides for the assembly of copper bars (manufactured through cold drawing, successive parting-off and eventual removal of material in excess) around opportune positioning cages. Then they proceed to the moulding of the thermosetting resin to fix the position of bars, to the milling to create voids on the head, the undercutting to eliminate insulating material present between one bar and the other, to turning to achieve the final geometry and, finally, to finishing operations. A technology that certainly allows implementing components that feature good performances and quality but nevertheless, still today, affected by a series of problems and criticalities among which the main ones concern: the use of a big quantity of raw material (copper) connected with the fact that the piece geometry is obtained by stock removal.

The need of removing the insulating material from the sliding surface of the brush (undercutting) which implies quite long machining times, due to the particular product geometry (accentuated head overhang), it is necessary to use cutters with very small diameter (about Ø 10mm) that perform a very low feed speed (scarce product productivity).
Moreover, the undercutting needs a very precise cut positioning, with the result of calling for level electronics (tracking mode cutting) and of producing anyway a certain quantity of non-compliant products.
The inner gripping of the commutator bar, realized through a big T-shaped protuberance, it too of copper, which notably increases the mass to be held while rotating.
Dealing with the current above-described survey, it is therefore obvious that the development guidelines of the reference market precisely converge towards an ever-growing demand for new technologies, for increasingly performing products at low costs. Research and development, strongly pursued by Cagnoni itself, over the last few years was aimed at studying, experimenting and developing an alternative technology to the conventional ones used by competitors today.
Such technology, which provides for cold moulding (instead of the traditional stock removal machining), will permit to manufacture copper head commutators (therefore optimizing the use of raw materials) with better final characteristics, lower industrial costs than those applied on the market today and with both economic-productive and environmental benefits.
Therefore, the company’s R&D department intends to create a different product/process from the present state-of-the-art.
Customized projects and virtual prototyping techniques
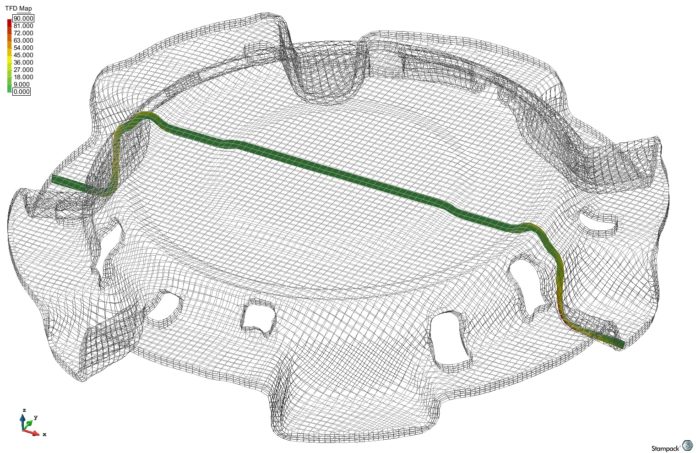
The use of virtual prototyping techniques allows competing and standing out in a market turning out to be increasingly dynamic and fast. The analysis of the stamping process through the finite element simulation allows assessing the relations among the various geometrical parameters of tool equipment and the necessary magnitudes to estimate the project validity; without implementing the numerous physical prototypes that would be necessary to succeed in defining correctly a method assuring the geometrical and dimensional tolerances demanded by customers.
This characteristic allows Bora, company headquartered at Moie di Maiolati Spontini (AN) that performs the activities of design, manufacturing and maintenance of tools (besides the sheet metal stamping of components for the automotive and household appliance industries), to offer a co-design service of the component together with final customers, thus reducing critical zones already in a preliminary phase; in addition to a drastic reduction of direct costs connected with the physical prototyping (design and implementation) and of the indirect costs linked with the testing phase.
Shaping the operations for perfect results
The main problems that generally emerge depend on the shape and on the characteristics of the piece to be implemented. In particular, for components characterized by small sizes compared to the thickness and by high deformation gradients, are critical the operations that affect the formability and the thickness reduction due to the deformation.

Using finite-element virtual simulation techniques and relying on the long-term experience gained by the company in the sector, it is possible to model correctly roughing and forming operations, to propose possible modifications of the element shape to the customer. This to improve the feasibility and the attainable thicknesses in short times while providing highly reliable indications. To the ends of a correct simulation of the stamping process, the company’s technical department manages both purely geometrical aspects (such as the shape of tools), and information about the material behaviour (by which are modelled the elastic response, the work hardening, the anisotropy and the formability diagram through the data provided by the supplier of raw materials), and dynamic aspects of the tool (such as the friction between the sheet metal and the various tools, the force and the position of the elastic members controlling the blank holders).
Impact on efficiency of core materials
No matter whether intended for a small or big household appliance, or used to drive hybrid and/or electrical cars or, moreover, applied in industrial ambits, the electric motor goes on confirming an unprecedented global growth trend.
Challenge that involves materials
Component manufacturers, producers and end users focus on this faster and faster diffusion, orienting their commitment not only to the reduction of costs but also to the optimization of performances and to the pursuit of the highest efficiency. A challenge that directly involves also the materials that constitute the core of electric cars, from the magnetic lamination to the stator pack.

We talked about that with Mr. Stefano Fortunati, Senior Technical Manager, Stainless Steel & Electrical Steel Metallurgy and manager of the Research Unit of CSM Terni, with specific focus on the “white good” and automotive sectors. «For several years now – explains Mr. Fortunati – efficiency has represented a key development factor, also to comply with the regulations provided on national and international scale. For this reason, the household appliance and automotive fields, as well as others, have paid ever-rising attention to the high efficiency of electric motors for a long time».
Approach, the latter, that has motivated and determined a production shift towards higher and higher quality classes.
«Including – underlines Mr. Fortunati – the producers of magnetic laminations used for the implementation of electric motor cores».
The decreasing demand for raw materials
A context that highlights, compared to the past, a decrease of the demand for less valuable raw materials (classes with very low percentage values of Silicon or similar) and of “high” thicknesses (even 0.65 mm).
The current trend is preferring, also in the “white goods” world, lamination thicknesses included between 0.5 and 0.35 mm, and steels characterized by a higher Silicon content. «Important aspect – underlines Mr. Fortunati – is also the higher care and the control of the crystalline microstructure, besides the choice and the selection of increasingly clean/pure steels (i.e. free from second non-metal phases)».
Actually, in fact, a low level of internal cleaning and purity, combined with a distribution of defects and second phases, increases the likelihood of constraints to the movement of magnetic domains during the magnetization. This implies a rise of losses and, therefore, an efficiency decrease.
The added-value of the magnetic permeability
«The demand coming from the market – adds Mr. Fortunati – consists then in the availability of raw materials with improved characteristics, precisely to enhance efficiency. It is undoubted that, from the point of view of the material research, this aspect represents a “driving force”. However, it is not sufficient for the attainment of the targets». It is relevant also the aspect of design and engineering change the electric motor is living. From a more general point of view, in the past the only (or anyway the main) key design parameter was represented by magnetic losses, by power losses.
«The progress and the design evolution – explains Mr. Fortunati – have led in time to recognize a higher value to the parameter of the material magnetic permeability. Material that, for applications on rotary machines, must assure an easy magnetization in isotropic manner in all directions of the plan of laminations constituting the ferromagnetic core». Concerning this, from the point of view of the material crystallography, it is necessary to grant that the (crystallographic) directions of easy magnetization are homogeneously distributed in the plan.
Relying on improved crystalline texture means enhancing the magnetic permeability to achieve higher applicative efficiency.
Given that and knowing that magnetic losses, heating and power losses occur in the core magnetization, it is important also to evaluate the necessary current intensity. Succeeding in magnetizing the conductive material optimally allows using a lower quantity of it.

«Moreover, also less – adds Mr. Fortunati – is the current that passes inside windings. This means reducing losses. An approach that considers not only the magnetic lamination, i.e. the ferromagnetic material inside the core and its behaviour. But also how much conductive material and the necessary current intensity to achieve the expected result».
A sign that shows and highlights the great liveliness that is permeating the design of electric motors. Of whatever typology they are (induction, synchronous, asynchronous, reluctance motors and so on).
A further guideline in the general development of motors, for both the household appliance sector, the automotive and industry in general is oriented towards the research of thinner and thinner materials.
Worth considering, then, the material resistivity element, faced choosing materials prevailingly beneficiated with Silicon but also with Aluminium or Manganese. With a limit, because increasing the widely used Silicon with values exceeding 3.5%, the material becomes too fragile, making their industrial manufacturing and their use very critical. Then, a further strategy consisted in orienting the research towards the improvement of the material surface quality and of its cleaning.
«Differentiating elements – underlines Mr. Fortunati – that however lead to a sort of selection among the steel mills that today can grant the production in conformity with these requisites».
The best compromise between thickness and purity
Thickness and electric resistivity (due to the content of Silicon, Aluminium and Manganese) represent determinant factors in automotive ambit, because the law that rules magnetic losses includes the frequency multiplier factor. In other words, in alternate field, their contribution becomes very important in industrial and/or domestic ambit.
«Even more determinant – underlines Mr. Fortunati – in the automotive industry, where they usually deal with variable frequencies and high frequencies, with a reference factor for the lamination characterization that reaches 400 Hz».
We should consider that the best attainable materials by a conventional chain feature magnetic losses (measured at an operation induction of 1.5 Tesla – 50 Hz, with reference thickness of 0.35 mm) with values around 2 W/kg.
Referring instead to the characterization of similar materials, optimized for automotive applications (measured at 400 Hz), such value notably increases, up to 14-15 W/kg.
Therefore, the general trend is demanding and finding better and better solutions in terms of losses and crystalline textures, to improve their polarizability, i.e. the magnetic permeability. Dominant factor, the latter, to obtain a higher power density.
As already underlined, all seem oriented towards increasingly thin materials but marked out by worse mechanical properties, then with a potential more difficult applicability in some ambits.
The electric resistivity
The other aspect and conflicting factor is represented by the percentage of elements that increase the electric resistivity (first of all Silicon) contained in the material. «If on one hand – explains Mr. Fortunati – they prefer materials with high alloy content to improve losses, on the other hand this intrinsically hinders the opportunity of increasing the magnetic permeability».

Today, then, it seems that research has chosen orienting the development of products with improved texture, possibly limiting the alloy content to grant a better magnetic permeability. And, meanwhile, acting on other awarding aspects to improve losses, such as steel cleaning, thickness and surface quality. «An improvement model, the latter, – notices Mr. Fortunati – more difficult to seize but leading in the future to products with better usability, for those working now at new motor projects and for the more and more challenging market requirements. Without forgetting that the trend towards the “ultra-thin” is not always positively judged by the manufacturers of cores and stator packs, owing to the sometimes critical necessary machining and more complex processes to be managed».
A glance at future trends
The current trend seems then to pursue the research of increasingly thin materials but we should consider right now the possible complications. It is then necessary to operate in parallel, for instance from the process point of view.
«Displacing for instance blanking – adds Mr. Fortunati – from mechanical systems towards solutions that adopt laser technologies, less affected by the thickness effect and that grant a minor degradation of the magnetic behaviour around the blanking/cutting areas. Meanwhile, we should imagine the manufacturing of super-thin laminations with a multilayer technology that can decrease the magnetic loss while facilitating their use».
Another element, anyway known for a long time, but really driving towards the smart use of these materials for applications such as household appliances but, especially in automotive ambit (where sizes and weights play a determinant role) is the stress control.
The role of stress control
When they design a motor, they tend in fact to obtain the best performances through the choice of the number of poles, number of teeth and so on, thus manufacturing a blank to implement the stator pack, even complex (with several cuts, slots and so on), compact and with very small sizes.

«Material – adds Mr. Fortunati – that must be produced at the best possible state, without internal residual mechanical stresses that negatively influence the magnetic behaviour. It is clear that the blanking operation and, more in general, assembling processes, generate mechanical stresses and residual deformations and, actually, they deteriorate the material, with effects that become serious proportionally to the high magnetic quality of the starting material».
The use of “semi-finished” materials
The manufacturers of electric machine cores can face this aspect exploiting a stress-relieving annealing, to be carried out after the implementation of the stator pack, compacted and provided with windings.
«This process phase – explains Mr. Fortunati – is prerogative only of some companies that, instead of treating non-oriented grain material called “fully-finished”, use “semi-finished” materials. In other words, materials manufactured at lower costs and typically with relatively low percentages of Silicon, supplied not in a finished state but annealed, not decarburized and further cold-rolled, with a very low deformation level. The successive static annealing of the assembled core carried out by the user is calibrated to complete the material purification and to obtain the desired crystalline microstructure».
The analysis of this type of structure, as delivered by the steel producer, shows initial very bad magnetic specifications. Nevertheless, the stator pack producer improves the intrinsic properties through annealing (performed according to particular treatments and parameters provided for by law), which transforms the inner structure and solves the problem of residual stresses, induced by cuts and assembling operations. A process, the latter, that facilitates a calculated metallurgic process and recovers optimal magnetic characteristics. These are the peculiarities that identify “semi-finished” materials, spread especially by geographical areas.
Concerning this, Japan and United States have registered their broad diffusion for some time now, unlike what is happening in Europe. We are referring to materials that, even if considered of not excellent qualitative level, combine the advantage of a lower Silicon percentage (then better magnetic permeability), with the plus of lower cost and the solution of the criticality dictated by blanking.
«I believe that this represents an interesting field of research and development – ends Mr. Fortunati – still according to the logic of finding the best and optimal compromise able to satisfy the entire manufacturing chain, from the producer of raw materials to the motor manufacturer».

Research and development activity where CSM (Centro Sviluppo Materiali) represents a qualified partner on a domestic and international scale, supporting constant innovation, process and product improvement and the attainment of higher and higher qualitative targets.
Experience and innovation at the service of materials
CSM (Centro Sviluppo Materiali) was established in 1963 as research centre of IRI in the steel industry. Today it represents the most important Italian private reality of RINA Group in the ambit of the innovation and improvement of product and process. A structure whose mission consists in developing and transferring, in industry and market at world level, the technological innovation in the strategic sector of materials and relative design, production and application technologies.
The innovation skills of CSM are based on the know-how gained in fifty years of industrial projects in metal and ceramic materials and in the integration of enabling technologies. Internet of Things, Additive Manufacturing, Big Data and Data Analytics, Augmented Reality, Collaborative Robotics and Digital Twins are some of the key words of the new context. The Centre can claim a long experience in these issues, achieved through innovation projects in the sector of materials, developed in collaboration with manufacturing companies of primary importance on a world scale.
Today CSM operates for the steel manufacturing industry and for diversified fields, such as oil and gas, aerospace, special materials and products, engineering and plant engineering, environment and energy. A strict collaboration with big, medium and small businesses, both engineering, manufacturing and service providers. All project phases, including simulations, preparations and analysis of samples and mock-ups, as well as all testing steps, take place in its own structures. Acknowledged as important pole of the European research and innovation network, CSM has always maintained a strong relation with steel partners at international level, too.
(Marcella Trapp)
How an electric motor works in a car
A three-phase, four-pole induction motor is made of two main parts: a stator and a rotor. The stator is made of three parts: a stator core, conducting wire, and frame. The stator core is a group of steel rings that are insulated from one another and then laminated together.
These rings include slots on their inside that the conducting wire will wrap around to form the stator coils. Simply put, in a three-phase induction motor, there are three different wire types. You can call these wire types Phase 1, Phase 2, and Phase 3.
Each wire type is wrapped around the slots on opposite sides of the inside of the stator core. Once the conducting wire is in place within the stator core, the core is placed within the frame.
How does an electric motor work?
Because of the complexity of the topic, the following is a simplified explanation of how a four-pole, three-phase AC induction motor works in a car. It starts with the battery in the car that is connected to the motor. Electrical energy is supplied to the stator via the car’s battery. The coils within the stator (made from the conducting wire) are arranged on opposite sides of the stator core and act as magnets, in a way. Therefore, when the electrical energy from the car battery is supplied to the motor, the coils create rotating, magnetic fields that pull the conducting rods on the outside of the rotor along behind it. The spinning rotor is what creates the mechanical energy needed to turn the gears of the car, which, in turn, rotate the tires. Now in a typical car, i.e., non-electric, there is both an engine and an alternator. The battery powers the engine, which powers the gears and wheels. The rotation of the wheels is what then powers the alternator in the car and the alternator recharges the battery. This is why you are told to drive your car around for a period after being jumped: the battery needs to be recharged in order to function appropriately. There is no alternator in an electric car.
So, how does the battery recharge then? While there is no separate alternator, the motor in an electric car acts as both motor and alternator.

This is due to the alternating nature of the AC signal that allows the voltage to be easily stepped up or stepped down to different values.That’s one of the reasons why electric cars are so unique.
As referenced above, the battery starts the motor, which supplies energy to the gears, which rotates the tires. This process happens when your foot is on the accelerator — the rotor is pulled along by the rotating magnetic field, requiring more torque. But what happens when you let off of the accelerator? When your foot comes off the accelerator the rotating magnetic field stops and the rotor starts spinning faster (as opposed to being pulled along by the magnetic field). When the rotor spins faster than the rotating magnetic field in the stator, this action recharges the battery, acting as an alternator.
Alternating current vs direct current
The conceptual differences behind these two types of currents should be obvious; while one current (DC) is consistent the other (AC) is more intermittent. However, things are a bit more complicated than just that simple explanation, so let’s break these two terms out in a bit more detail.
Direct current (DC)
The continuous current refers to a constant and unidirectional electric flow. Furthermore, the voltage keeps the polarity in time. On batteries, in fact, it is clearly marked which the positive and negative poles is. These use the constant potential difference to generate a current always in the same direction. In addition to batteries, fuel cells and solar ones, also the sliding between specific materials can produce direct current.
Alternating current (AC)
The term alternating current defines a type of electricity characterized by voltage (think water pressure in a hose) and current (think rate of water flow through the hose) that vary with respect to time (fig. 1). As the voltage and current of an AC signal change, they most often follow the pattern of a sine wave. Due to the waveform being a sine wave, the voltage and current alternate between a positive and negative polarity when viewed over time. The sine wave shape of AC signals is due to the way in which the electricity is generated.
Another term you may hear when discussing AC electricity is frequency. The frequency of the signal is the number of complete wave cycles completed during one second of time. Frequency is measured in Hertz (Hz) and in the United States the standard power-line frequency is 60 Hz. This means that the AC signal oscillates at a rate of 60 complete back-forth cycles every second.
Why is this important?
AC electricity is the best way to transfer useable energy from a generation source (i.e., a dam or windmill) over great distances.

This is due to the alternating nature of the AC signal that allows the voltage to be easily stepped up or stepped down to different values.This is why your home’s outlets will say 120 volts AC (safer for human consumption) but the voltage of a distribution transformer which supply power to a neighborhood (those cylindrical grey boxes you see on the power line poles), might have voltage as high as 66 kVA (66,000 volts AC).
AC power allows us to construct generators, motors, and distribution systems from electricity that are far more efficient than direct current, which is why AC is the most popular energy current for powering applications.
How does a three-phase, four-pole induction motor work?
Most large, industrial motors are induction motors and they are used to power diesel trains, dishwashers, fans, and countless other things. However, what exactly does an “induction” motor mean?
In technical terms, it means that the stator windings induce a current to flow into the rotor conductors.
In layman’s terms, this means that the motor is started because electricity is induced into the rotor by magnetic currents instead of a direct connection to electricity, like other motors such as a DC commutator motor.
What does polyphase mean? Whenever you have a stator that houses multiple, unique windings per motor pole, you are dealing with polyphase (fig. 2).
It is most common to expect a polyphase motor to be made up of three phases, but there are motors that utilize two phases. A polyphase system uses multiple voltages to phase-shift apart from each one in order to go intentionally out of line.

What does three phase mean? Based around Nikola Tesla’s basic principles defined in his polyphase induction motor put forth in 1883, “three phase” refers to the electrical energy currents that are supplied to the stator via the car’s battery (fig. 3).
This energy causes the conducting wire coils to start to behave like electromagnets. A simple way to understand three phase is to consider three cylinders, shaped in a Y formation, utilizing energy pointed toward the center point to generate power. As the energy is created, the current flows into the coil pairs inside the engine in such a way that it naturally creates a north and south pole within the coils, allowing them to act like opposite sides of a magnet.
Top performing electric cars
As this technology continues to advance, the performance of electric cars are starting to quickly catch up to, and even outperform, their gas counterparts. While there remains some distance for electric cars to go, the leaps that companies like Tesla and Toyota have made to this point have inspired hope that the future of transportation will no longer be reliant on fossil fuels. At this point, we all know the success that Tesla is experiencing in the field, putting out the Tesla Model S Sedan that is capable of driving up to 288 miles, hitting 155 MPH, and has 687 lb-ft torque.
However, there are dozens of other companies that are seeing massive progress in the field, such as Ford’s Fusion Hybrid, Toyota’s Prius and Camry-Hybrid, Mitsubishi’s iMiEV, Ford’s Focus, BMW’s i3, Chevy’s Spark, and Mercedes’ B-Class Electric (fig. 4).
Electric cars and the environment
Electric engines impact the environment both directly and indirectly at a micro and macro level. It depends on how you want to perceive the situation and how much energy you want. From the individual standpoint, electric cars do not require gasoline to run, which leads to cars with no emissions populating our highways and cities. While this presents a new problem with additional burden of electricity production, it alleviates the strain from millions of cars densely populating cities and suburbs putting toxins into the air (fig. 5).
Note: The MPG (miles per gallon) values listed for each region is the combined city/highway fuel economy rating of a gasoline vehicle that would have global warmings equivalent to driving an EV. Regional global warming emissions ratings are based on 2012 power plant data in the EPA’s eGrid 2015 database. Comparisons include gasoline and electricity fuel production emissions. The 58 MPG U.S. average is a sales-weighted average based on where EV’s were sold in 2014. From a large-scale perspective, there are several benefits to the rise of electric cars.

For starters, there is a reduction in noise pollution as the noise emitted from an electric engine is far more subdued than that of a gas-powered engine. In addition, because electric engines do not require the same type of lubricants and maintenance that a gas engine does, the chemicals and oils used at auto-shops will be reduced due to fewer cars needing check-ups.
Conclusion
The electric engine is changing the course of history in the same way that the steam powered engine and printing press redefined progress. While the electric engine is not paving new grounds in the same vein as these inventions, it is opening up a brand new segment of the transportation industry that is not only focused on style and performance, but also external impact. So, while the electric engine may not be reforming the world due to an introduction of some brand new invention or the creation of a new marketplace, it is redefining how we as a society define progress. If nothing else is to come from the advancements with the electric engine, at the very least we can say that our society has moved forward with our awareness of our environmental impact. This is the new definition of progress, as defined by the electric engine.
(Jill Scott)