Safety is crucial for electric vehicles (EVs) due to the high energy density of lithium-ion batteries, which can pose risks if operating conditions deviate. A Battery Management System (BMS) is essential to prevent issues like thermal runaway, an uncontrollable reaction that can destroy the battery. The BMS monitors current, voltage, and temperature, prevents overcharge and discharge, balances cell charge, estimates the battery’s state of charge (SOC) and health (SOH), and controls temperature. These functions are vital for performance, safety, battery longevity, and user experience. For instance, preventing overcharge and discharge helps avoid premature battery aging, maintaining vehicle performance over time.
Benefits of Simulation in BMS Development
Engineers use desktop simulation to model the battery, environment, and BMS algorithms, allowing them to explore new designs and test system architectures before hardware prototyping. This process verifies BMS design functions, like evaluating balancing configurations and testing system behavior during faults. Once validated, engineers generate C or HDL code for rapid prototyping (RP) or hardware-in-the-loop (HIL) testing, further validating BMS algorithms in real-time. RP involves deploying code to a real-time computer mimicking the production microcontroller. Automatic code generation allows algorithm changes to be tested quickly. HIL testing uses battery plant models to create a virtual environment representing the battery pack and system components, enabling real-time BMS controller validation before hardware development.
Simulation significantly reduces design-to-code generation time, enhancing modeling speed and efficiency. Altigreen Propulsion Labs used simulation to iteratively test SOC estimation techniques, such as Kalman filtering and Coulomb counting, designing a comprehensive SOC estimation method. Prathamesh Patki, Principal Engineer at Altigreen, notes that “Embedded Coder® has cut development time in half,” allowing rapid implementation on real hardware.
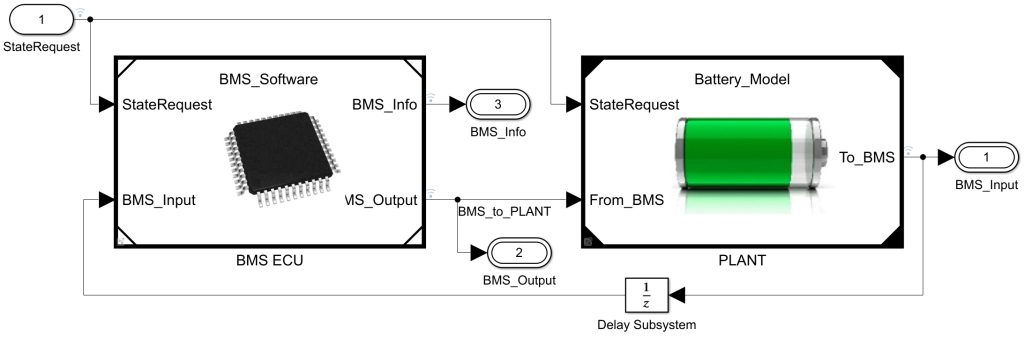
Modeling and Simulation Use Cases in BMS Development
Cell characterization involves fitting a battery model to experimental data, crucial for setting BMS control parameters like those of a Kalman Filter for SOC estimation. The same battery model is used for system-level simulations later in development. Tools like Simscape™ Battery™ offer various battery modeling approaches, including equivalent circuit and electrochemical modeling.
Fast charging is a key EV performance indicator but stresses battery materials, reducing lifespan. Simulation and optimization are used to optimize fast charging power profiles, minimizing charging time while keeping stress within acceptable limits.
Production code generation aligns with formal certification standards in the automotive industry. For example, when LG Chem developed the BMS for the Volvo XC90 plug-in hybrid, AUTOSAR compliance was required. Modeling and simulation were integral to their design workflow, reducing software issues significantly. The BMS achieved ISO 26262 certification for Automotive Safety Integrity Level C (ASIL C).
Conclusion
Modeling and simulation in BMS design enable faster development, reduced costs, and safer, more efficient EVs. By testing BMS algorithms under various conditions, engineers ensure the software handles real-world scenarios, reducing costly testing. This approach ensures products exceed industry standards and consumer expectations.
For additional resources on Electrification, visit mathworks.com
(by Danielle Chu, Senior Product Marketing Manager, MathWorks)