Among the various way to control electrical motor movement, the field oriented control and closed-loop motor control are the most viable to get accuracy and efficiency.
Field oriented control (FOC) is the most efficient way to drive motors. It transforms actual phase currents from stator-fixed to field-synchronous coordinate systems by using two mathematical transformations. The resulting coordinate system has only two dimensions (magnetic flux and torque), which are orthogonal components and can be visualized as a vector; hence FOC may sometimes be called vector control. FOC was originally developed for high end applications and has traditionally been difficult to implement. Trinamic technology from Analog Devices Inc (ADI), offers FOC as an easy-to-use hardware building block.
Field oriented control (FOC) uses current control to manage the torque of 3-phase motors and stepper motors with high accuracy and bandwidth. Using orthogonal applied current to drive electrical motors it is the most efficient way to control permanent magnet synchronous motors such as 3-phase BLDC motors (Brushless DC electric motor) or two-phase stepper motors.
Servo controllers are key in industry applications with synchronous drives. By integrating FOC into hardware, ADI Trinamic technology gives engineers the building blocks to reduce servo controller design time and complexity.
The ways to electrical motor control: how FOC works
To generate a precise amount of torque, it’s not enough to control the amount of current needed to generate the specific target torque but it’s also necessary to phase the magnetic field of the magnets in the rotor.
Applying current in phase to the magnetic field does not generate torque, but orthogonal applied current does. FOC answers this challenge by using orthogonal applied current to drive electric motors with maximum efficiency using real-world current and rotor position information.
In a FOC-driven electrical motor, the exact position of the rotor determines the orthogonal current IQ that must be applied to accurately control the next step. In other words, the orthogonal current IQ controls the motor by knowing the exact position of the rotor.
Finding Vectors for FOC
Field-oriented control is also called vector control because it can be used to obtain IQ and provide simple-to-use control values in a single vector. Rotors are controlled by applying voltages to three sinusoidal motor current phases or in the case of stepper motors by applying voltage to two sinusoidal motor current phases. The applied voltages result in a current flow through the motor, generating a magnetic field and therefore attracting the magnetic rotor into the desired position. FOC simplifies this approach by transforming currents and voltages.
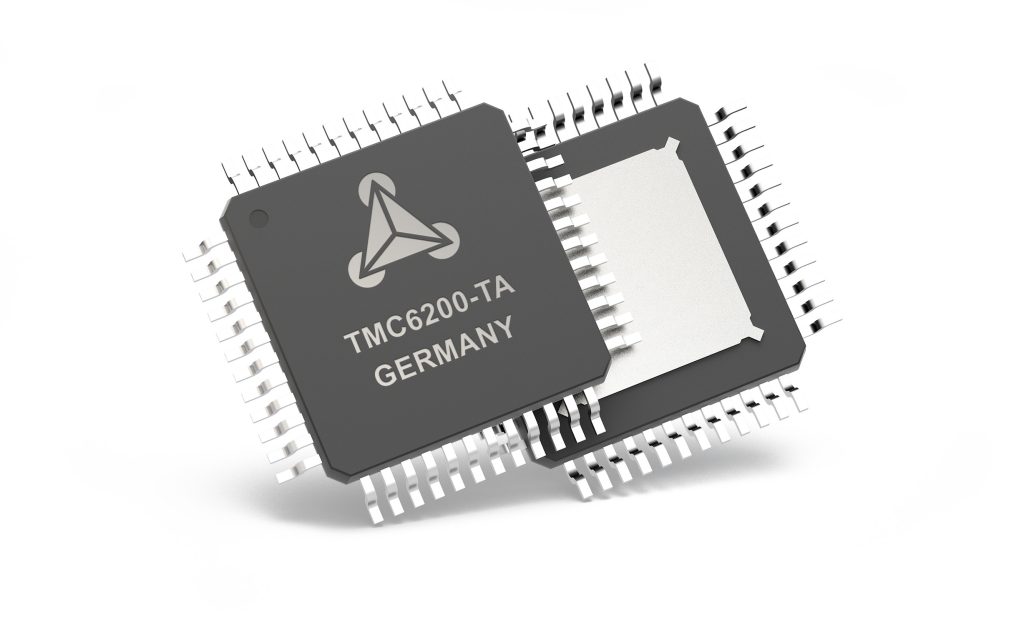
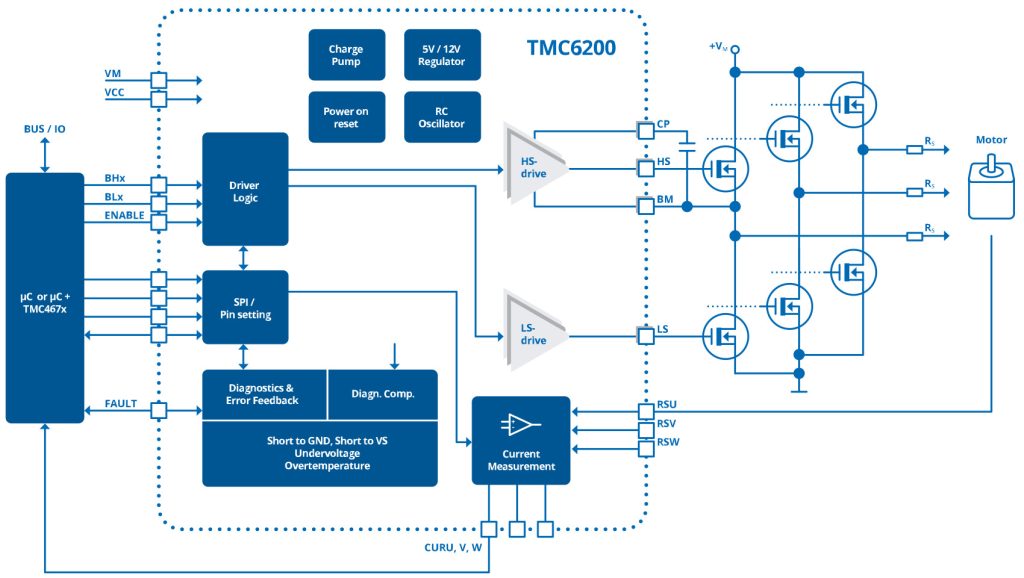
The result is a representation of the current as a single vector that is defined by the orthogonal components IQ and ID. Two mathematical transformations called Clarke and Park are used to find this vector by transforming the actual phase currents from stator-fixed to field-synchronous coordinate systems. IQ and ID are phasor components of the armature current. The IQ component is in phase with the generated armature voltage and produces a magnetic flux that is centered on the space between the permanent-magnet field poles. ID produces a magnetic flux that is centered on the permanent magnet poles.
Motor control
With FOC, two PI (Proportional and Integral) current controllers can be used to control both aspects of the motor current vector separately. One current controller (IQ) is used to control the motor’s torque and is thereby called the torque controller; the other one (ID) controls the magnetic flux inside the motor. Transformations are based on the actual rotor angle, which is acquired by position sensors like Hall sensors or encoders. The magnetic flux is mainly generated by the rotor, so its target value is usually zero.
Servo control adds speed and position controllers to this architecture to make it fully functional for positioning applications. All controllers require proper feedback to work at high dynamics and to compensate for unknown load forces. For current controllers, this means that the coil currents need to be measured. Position can be measured with encoders or roughly with Hall sensors. As velocity sensors are not common, the velocity of the motor is often computed by differentiation of the position signal.
Closed-loop motor control
Closed-loop motor control provides direct feedback about how a motor is behaving in real conditions and not just how it should behave according to the system; the feedback it is used to improve performance, safety, and efficiency.
Motion control without feedback from the motor assumes that motors always behave as expected. In reality, various aspects of a mechanical system can influence a motor. Even the user itself can affect motor behavior, for example by accidentally hitting a robotic arm or picking up a 3D printer while it’s printing. For stepper motors under common conditions, the position of the motor is deterministic and predictable. To cover uncommon conditions, motor feedback systems can be implemented to create powerful servo drive systems for stepper motors or to add positioning functionality to BLDC drives.
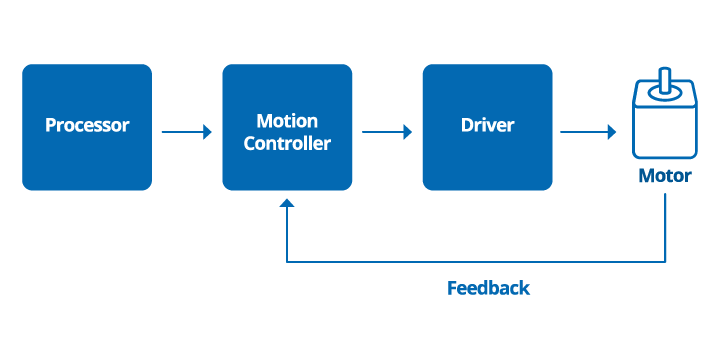
Contrary to open-loop systems, closed-loop motor control is designed to automatically achieve the target output condition and maintain it by feeding back the actual state of the motor, such as velocity or position. Whenever motor feedback is processed, it is a closed-loop system. That’s why it’s also called feedback control.
There are various ways to close the loop in a motor drive system, like using sensors or encoders. Another option is to sense the motor’s electrical behavior since the power consumption is directly related to the axis’ load. Analog Devices provides a variety of sensors and encoders that can be used to create a safer, more efficient closed-loop motor control system.
Analog and digital Hall sensors
An analog Hall sensor measures the strength of a magnetic field and provides an output voltage proportional to it. To protect the Hall sensor from being damaged by large magnetic fields, the amplifier will saturate before reaching the limits of the power supply.
Contrary to analog Hall sensors, a digital Hall sensor only provides two outputs: ON or OFF. The digital output is compared to a preset reference and when this reference is exceeded, the output will turn on. As long as the output of the Hall sensor is below the reference point, the output is off.
Placing a magnet at the back of a rotor and a magnetic sensor IC close to that magnet creates a feedback system showing the rotor’s absolute position without taking up much space. While not suited for higher velocities or applications demanding a high resolution, magnetic encoder ICs are a cost-effective closed-loop solution with acceptable feedback for many systems. To avoid any alignment errors, it’s important to mount both the sensor IC and magnet accurately. ADI Trinamic technology offers a plug-and-play solution in its SensOstep technology and PANdrive smart motors.
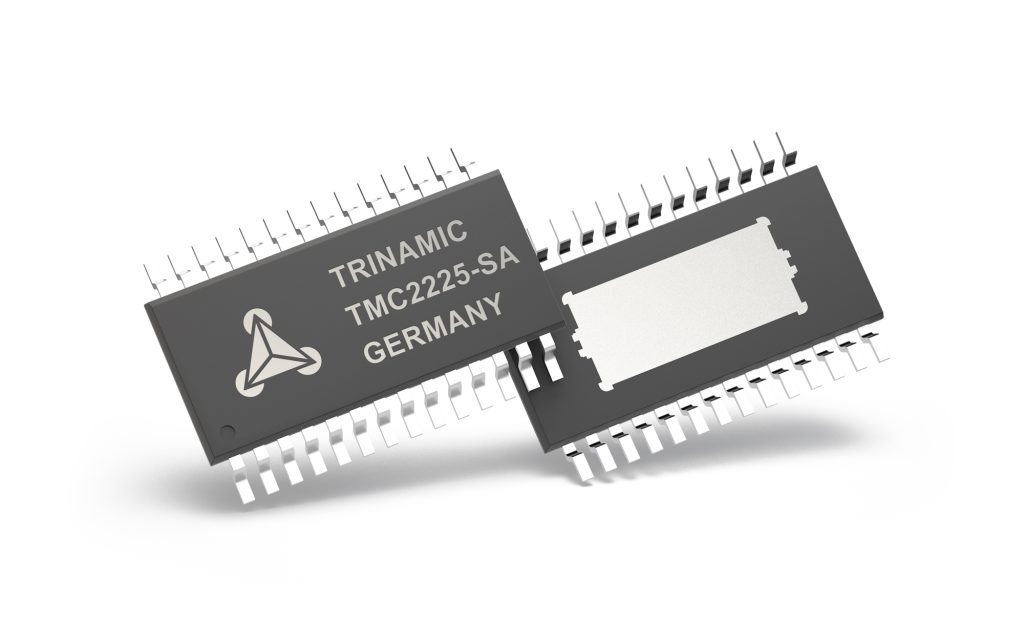
Incremental encoders
Incremental encoders can be used to keep track of a motor’s position and to determine its velocity. Using an encoder disc and optical sensors, incremental encoders provide motor feedback by generating an output signal for each incremental step. That’s why they’re also known as optical encoders.
Incremental encoders typically have two output signals, A and B. These are mounted at a 90-degree offset to each other so that rotation and direction of the encoder can be detected (A before B, or B before A). A third output signal can be added as a reference point that only appears once per full rotation.
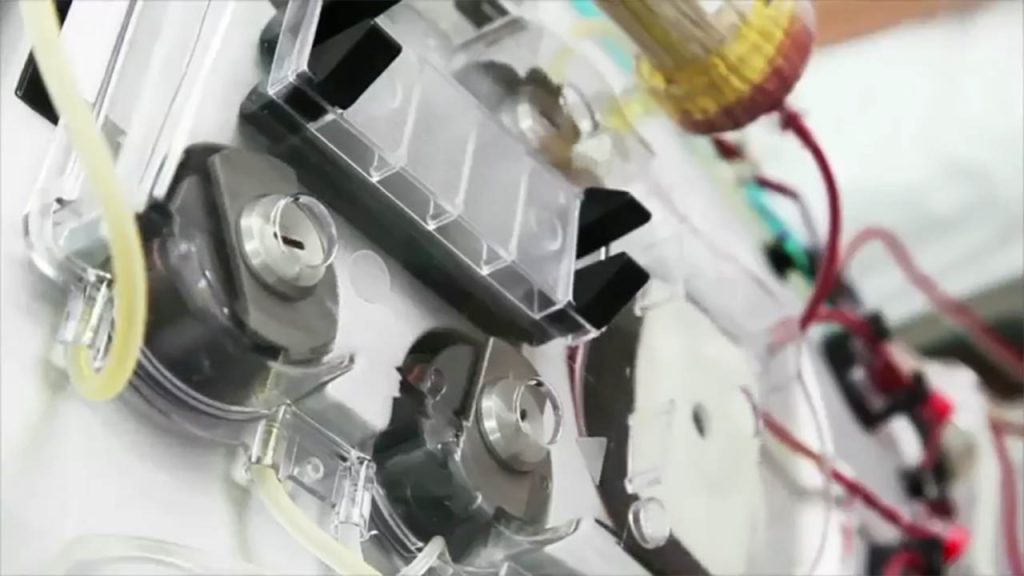
Current sensing detects current and converts it, generating an output voltage directly proportional to the current in the desired direction. A shunt or Hall effect current sensor can be used to sense the current at either the high-side, inline, or bottom. The detected values can also be stored for later use, including monitoring system behavior. This makes current sensing a cost-effective and reliable method for monitoring equipment status, increasing safety, and detecting unusual behavior.
ADI’s Trinamic motor and motion control products transform digital information into precise physical motion, enabling Industry 4.0 performance in applications such as advanced robotics, automation, medical prosthetics, 3D printing, and more. The ADI Trinamic portfolio includes motors, encoders, and motor control ICs and modules. These complete, efficient, small footprint solutions can help reduce complexity and time to market for intelligent motion systems while supporting potential space and performance efficiency improvements.
The ADI Trinamic portfolio offers an extensive set of tools to set up and fine-tune intelligent motor and motion control systems: A free and intuitive integrated development environment, CANopen tools, and ADI Trinamic technology access package (including the ADI Trinamic API). Regardless of MCU selection and programming style, ADI Trinamic technology offers industry software solutions that are ready to integrate into any firmware project.
(by Dario Gozzi)